Inorganic composite plate and preparation and use thereof
An inorganic composite and plate technology, applied in wood treatment, impregnated wood, manufacturing tools, etc., can solve the problems of floor performance limitations, increased costs, and unfavorable environmental protection, etc., to achieve improved mechanical properties, uniform distribution of powder particles, and reduced quality Effect
- Summary
- Abstract
- Description
- Claims
- Application Information
AI Technical Summary
Problems solved by technology
Method used
Image
Examples
Embodiment 1
[0029] Use basswood as raw material to make composite panels: The first step: Take 49.69 grams of solid NaOH and 14.91 grams of solid Na 2 SO 3 Mix and add water to prepare 1632mL alkaline cooking liquor; take 4 pieces of linden wood with a total dry mass of 496.87g and a volume of 320mm×170mm×5mm, and put them in the cooking liquor at 120℃ and cook for 3 hours; the second step : Put the boiled linden wood pieces in clean water and fully soak them at room temperature for 48 hours; the third step: vacuum-dry the soaked linden wood pieces at 90℃ to a moisture content of 12%; the fourth step : Dilute the above silica sol solution into a silica sol solution with a mass percentage concentration of 12%, take out 1632 mL, add 6.55 g of solid penetrant sodium dodecylbenzene sulfonate, so that the solid penetrant sodium dodecylbenzene sulfonate is in The mass percentage concentration in the silica sol solution is 0.4%; the fifth step: immerse the dried basswood monolith in the silica sol s...
Embodiment 2
[0031] Use basswood as raw material to make composite boards: The first step: take 39.74 grams of solid NaOH and 9.94 grams of solid Na 2 SO 3 Mix and add water to prepare 2176mL alkaline cooking liquor; take 4 pieces of linden wood with a total dry mass of 496.87g and a volume of 320mm×170mm×5mm, and put them in the cooking liquor at 130℃ and cook for 1.5 hours; the second step : Put the boiled linden wood pieces in clean water and fully soak them at room temperature for 36 hours; the third step: vacuum-dry the soaked linden wood pieces at 80°C to a moisture content of 15%; the fourth step : Dilute the above silica sol solution into a silica sol solution with a concentration of 10% by mass, take out 2176 mL, add 13.13 grams of solid penetrant sodium dodecyl benzene sulfonate, so that the solid penetrant sodium dodecyl benzene sulfonate is in The mass percentage concentration in the silica sol solution is 0.6%; the fifth step: immerse the dried basswood monolith in the silica sol ...
Embodiment 3
[0033] Use basswood as raw material to make composite panels: The first step: Take 44.72 grams of solid NaOH and 12.42 grams of solid Na 2 SO 3Mix and add water to prepare 1959mL alkaline cooking liquor; take 4 pieces of linden wood with a total dry mass of 496.87g and a volume of 320mm×170mm×5mm, and put them in the cooking liquor at 100℃ and cook for 2.5 hours; the second step : Put the boiled linden wood pieces in clean water and fully soak them at room temperature for 24 hours; the third step: vacuum-dry the soaked linden wood pieces at 80℃ to a moisture content of 10%; the fourth step : Dilute the above silica sol solution into a silica sol solution with a concentration of 20% by mass, take out 1959 mL, add 11.82 grams of solid penetrant sodium dodecyl benzene sulfonate to make the solid penetrant sodium dodecyl benzene sulfonate in The mass percentage concentration in the silica sol solution is 0.5%; the fifth step: immerse the dried basswood monolith in the silica sol solut...
PUM
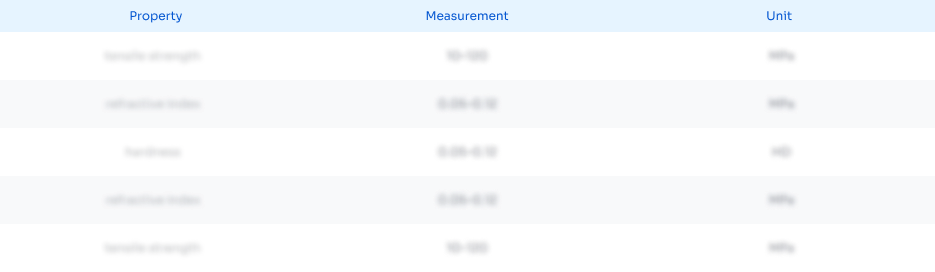
Abstract
Description
Claims
Application Information

- R&D
- Intellectual Property
- Life Sciences
- Materials
- Tech Scout
- Unparalleled Data Quality
- Higher Quality Content
- 60% Fewer Hallucinations
Browse by: Latest US Patents, China's latest patents, Technical Efficacy Thesaurus, Application Domain, Technology Topic, Popular Technical Reports.
© 2025 PatSnap. All rights reserved.Legal|Privacy policy|Modern Slavery Act Transparency Statement|Sitemap|About US| Contact US: help@patsnap.com