Motor controller and motor control system
A control device and control system technology, applied in the direction of motor control, motor generator control, AC motor control, etc., can solve problems such as unsuitable resonance characteristics
- Summary
- Abstract
- Description
- Claims
- Application Information
AI Technical Summary
Problems solved by technology
Method used
Image
Examples
no. 1 Embodiment approach
[0070] Using the block diagram of FIG. 4, a motor control system which is an embodiment of the present invention will be described. FIG. 4 shows an embodiment in which the optimal speed controller gain and position controller gain can be set according to the mechanical characteristics of the load that varies from time to time through the automatic tuning process even in the normal operating state of the device. Hereinafter, this embodiment will be described in detail.
[0071] In FIG. 4, the motor control system 200 includes: a motor 1; a load 2 driven by the motor 1; a connecting shaft 3 that connects the motor 1 and the load 2; a power converter 4 that drives the motor 1; Shaft, output the position detection value θ of the rotating shaft of the motor 1 M The position detector 27; the current detector 6 that detects the current flowing through the motor 1; and the motor control device 100.
[0072] The motor control device 100 includes: a speed calculator 5; a current controller ...
no. 2 Embodiment approach
[0152] The first embodiment adopts the q-axis current command Iq * To calculate the motor torque value τ input to the auto-tuning unit 11 M , The torque current detection value Iq can also be used for calculation.
[0153] In FIG. 10, the motor control system 210 of the second embodiment includes a motor control device 110, the motor control device 110, and the torque current detection value Iq is multiplied by the torque constant corresponding to the motor 1 through the amplifier 240, To calculate the motor torque value τ M .
no. 3 Embodiment approach
[0155] Next, the third embodiment of the present invention will be described using FIG. 11. In contrast to the first embodiment, the motor control device 120 of the third embodiment has a structure in which the vibration damping controller 16 is inserted between the position command generator 17, the position controller 14, and the subtractor. In other words, the damping controller 16 and the subtractor 15 are provided between the position command generator 17 and the position controller 14.
[0156] The damping controller 16 has the motor position detection value θ M As input signal, output load position estimated value θ L The load position estimator 23 of ^ provides its transfer characteristics by equation (39).
[0157] θ L ^=θ M ·(2ζ a ^ω a ^·s+ω a ^) / (s 2 +2ζ a ^ω a ^s+ω a ^ 2 )·······················(39)
[0158] The subtractor 24 receives the vibration control input command value θ from the position command generator 17 M ** Subtract the estimated load position θ L ^, cal...
PUM
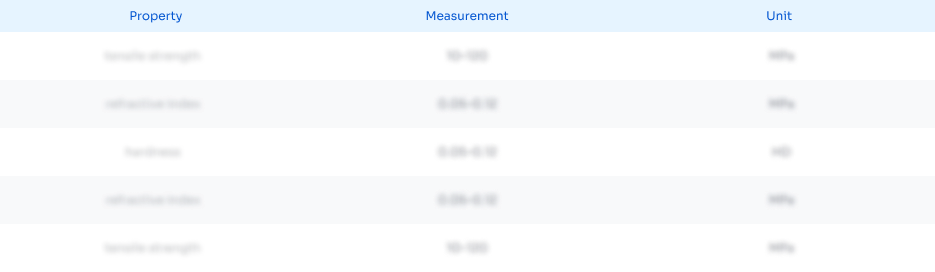
Abstract
Description
Claims
Application Information

- R&D
- Intellectual Property
- Life Sciences
- Materials
- Tech Scout
- Unparalleled Data Quality
- Higher Quality Content
- 60% Fewer Hallucinations
Browse by: Latest US Patents, China's latest patents, Technical Efficacy Thesaurus, Application Domain, Technology Topic, Popular Technical Reports.
© 2025 PatSnap. All rights reserved.Legal|Privacy policy|Modern Slavery Act Transparency Statement|Sitemap|About US| Contact US: help@patsnap.com