In-situ synthesis of high-pure green 6H-SiC
An in-situ synthesis, high-purity technology, applied in the field of in-situ synthesis of high-purity green SiC, can solve the problems that threaten the development of high-grade green silicon carbide, the reserves will be less and less, and the future development constraints, etc., to achieve the elimination of SO2 gas and The effects of high concentration brown smoke, reduced raw material input, and reduced industrial waste gas
- Summary
- Abstract
- Description
- Claims
- Application Information
AI Technical Summary
Problems solved by technology
Method used
Image
Examples
Embodiment Construction
[0015] As shown in the figure, the in-situ synthesis of high-purity green 6H-SiC according to the present invention is to combine 0.62-0.65 parts of anthracite carbon-based material (particle size is 10-30 μ, ash content88%), Quartz sand 0.98-1.02 parts (grain size is 50-80μ, SiO 2 >98.5%), 0.20-0.25 parts of silicon carbide and silicon oxide composite material (particle size is 2-5μ) and 0.10-0.15 parts of auxiliary industrial salt (NaCl>97%) are fully mixed (in order to ensure the physical-chemical For the smooth progress of the effect, the raw materials should be fully mixed, and the mixing time should not be less than 10 minutes each time) to prepare the reaction material; 1.90-2.00 parts of anthracite (particle size is 10mm, ash content 4-6%) and quartz sand 2.80-3.10 parts (particle size less than 1mm, SiO 2 >98%) are mixed evenly to prepare a mixed thermal insulation material, so that the ratio between the prepared mixed thermal insulation material and the reaction mat...
PUM
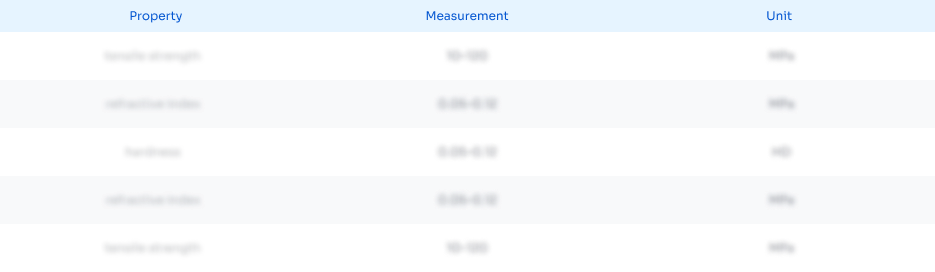
Abstract
Description
Claims
Application Information

- Generate Ideas
- Intellectual Property
- Life Sciences
- Materials
- Tech Scout
- Unparalleled Data Quality
- Higher Quality Content
- 60% Fewer Hallucinations
Browse by: Latest US Patents, China's latest patents, Technical Efficacy Thesaurus, Application Domain, Technology Topic, Popular Technical Reports.
© 2025 PatSnap. All rights reserved.Legal|Privacy policy|Modern Slavery Act Transparency Statement|Sitemap|About US| Contact US: help@patsnap.com