Mixing milling squeezing granulation units melt control valve
A technology of extrusion granulation and valve control, applied in valve details, multi-way valves, safety valves, etc., can solve problems such as lengthening of molten material channels, unfavorable process control, and increased energy consumption, and achieve low processing and manufacturing costs. The effect of compact structure and small footprint
- Summary
- Abstract
- Description
- Claims
- Application Information
AI Technical Summary
Problems solved by technology
Method used
Image
Examples
Embodiment Construction
[0017] As shown in Figure 1, it is the melt control valve of the mixing extrusion granulation unit in abnormal working state. Under the action of the oil cylinder (not shown) on the spool 3 upper end of the driving valve, the spool moves upwards to communicate with the 90-degree waste material bend channel 4 of the melt control valve runner 5 and the spool of the driving valve. Figure 2 shows that when it is working normally, the spool moves downward, so that the flow channel 5 of the melt control valve communicates with the straight channel 6 of the drive valve spool, so that the material enters through the flow channel of the control valve and the straight channel of the drive valve. Melt channel 8. As shown in accompanying drawing 3, a rotating shaft 9 is installed in the flow channel 5 of the regulating valve, and the alloy steel valve core 1 or valve plate with a wear-resistant and corrosion-resistant surface is fixed on the rotating shaft through a key. Manual or manual...
PUM
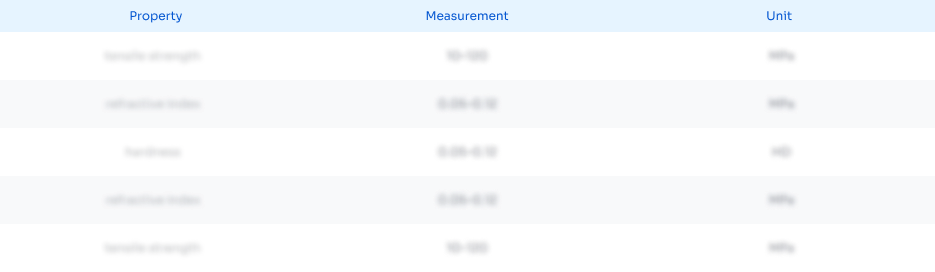
Abstract
Description
Claims
Application Information

- Generate Ideas
- Intellectual Property
- Life Sciences
- Materials
- Tech Scout
- Unparalleled Data Quality
- Higher Quality Content
- 60% Fewer Hallucinations
Browse by: Latest US Patents, China's latest patents, Technical Efficacy Thesaurus, Application Domain, Technology Topic, Popular Technical Reports.
© 2025 PatSnap. All rights reserved.Legal|Privacy policy|Modern Slavery Act Transparency Statement|Sitemap|About US| Contact US: help@patsnap.com