Fire box of inverse push type destructor
A waste incinerator and furnace technology, applied in the direction of incinerator, combustion method, combustion type, etc., can solve the problems that affect the stability of the incinerator, reduce the processing capacity of the incinerator, and the garbage cannot be completely burned, and achieve the best heat radiation effect Excellent, improve the utilization rate of garbage, shorten the burning time
- Summary
- Abstract
- Description
- Claims
- Application Information
AI Technical Summary
Problems solved by technology
Method used
Image
Examples
Embodiment 1
[0017] Accompanying drawing is the real structural representation of the present invention, as shown in the figure: the reverse thrust type refuse incinerator hearth of the present invention, comprises left and right side wall, front wall 3, rear wall 4 and fire grate 1 at the bottom, garbage inlet 2 It is arranged at the lower part of the front wall 3, and the ash outlet 5 is arranged at the lower part of the rear wall 4. The included angle θ1 between the front wall 3 and the horizontal plane is 13.5°. The included angle θ2 between 41 and the horizontal plane is 42°, and the included angle θ3 between the upper part 42 of the rear wall 4 and the horizontal plane is 104°.
Embodiment 2
[0019] Accompanying drawing is the real structural representation of the present invention, as shown in the figure: the reverse thrust type refuse incinerator hearth of the present invention, comprises left and right side wall, front wall 3, rear wall 4 and fire grate 1 at the bottom, garbage inlet 2 It is arranged at the lower part of the front wall 3, and the ash outlet 5 is arranged at the lower part of the rear wall 4. The included angle θ1 between the front wall 3 and the horizontal plane is 10°. The angle θ2 between the lower portion 41 and the horizontal plane is 38°, and the angle θ3 between the upper portion 42 of the rear wall 4 and the horizontal plane is 102°.
Embodiment 3
[0021] Accompanying drawing is the real structural representation of the present invention, as shown in the figure: the reverse thrust type refuse incinerator hearth of the present invention, comprises left and right side wall, front wall 3, rear wall 4 and fire grate 1 at the bottom, garbage inlet 2 It is arranged at the lower part of the front wall 3, and the ash outlet 5 is arranged at the lower part of the rear wall 4. The included angle θ1 between the front wall 3 and the horizontal plane is 15°. The angle θ2 between 41 and the horizontal plane is 45°, and the angle θ3 between the upper part 42 of the rear wall 4 and the horizontal plane is 110°.
[0022] Of course, the above embodiment is only for more clearly describing the present invention, and can not limit the protection scope of the present invention, for example, the angle θ1 of front wall 3 and horizontal plane can be any numerical value in 10 °-15 °; The angle θ2 between the lower part 41 and the horizontal plan...
PUM
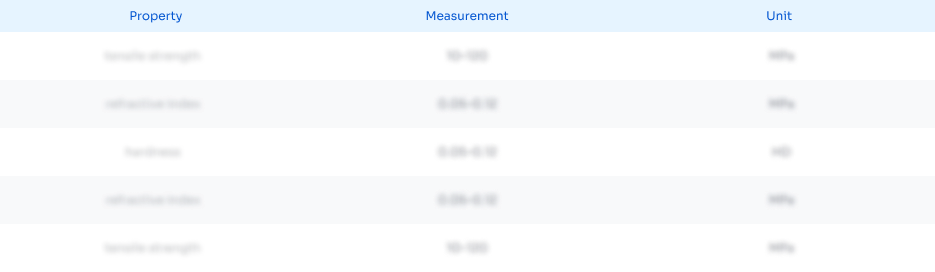
Abstract
Description
Claims
Application Information

- Generate Ideas
- Intellectual Property
- Life Sciences
- Materials
- Tech Scout
- Unparalleled Data Quality
- Higher Quality Content
- 60% Fewer Hallucinations
Browse by: Latest US Patents, China's latest patents, Technical Efficacy Thesaurus, Application Domain, Technology Topic, Popular Technical Reports.
© 2025 PatSnap. All rights reserved.Legal|Privacy policy|Modern Slavery Act Transparency Statement|Sitemap|About US| Contact US: help@patsnap.com