Plastic capillary pad, method and apparatus for producing the same
A capillary and plastic technology, which is applied in the field of manufacturing plastic capillary pads and equipment for manufacturing plastic capillary pads, can solve problems such as large assembly costs, tube connection damage, leakage, etc., and achieve good mechanical stress and strengthen the connection effect
- Summary
- Abstract
- Description
- Claims
- Application Information
AI Technical Summary
Problems solved by technology
Method used
Image
Examples
Embodiment Construction
[0030] [30] First, the entire structure of the capillary pad 1 according to the present invention will be described with reference to FIG. 1.
[0031] [31] The capillary pad 1 includes two manifolds 2, which are connected by a plurality of parallel capillaries 3. The collecting pipe 2 has connection joints 4 at the ends respectively, and the collecting pipe can be connected to the heating fluid circuit and the cooling fluid circuit through the connection joints. When the capillary pad 1 is working, the heating fluid or the cooling fluid flows into one of the two manifolds 2. The heating fluid or the cooling fluid flows from the aforementioned manifold 2 through the capillary tube 3 to the other manifold 2. The heating fluid or cooling fluid flows from the second manifold 2 back into the heating fluid circuit and the cooling fluid circuit. The capillary pad 1 is installed, for example, in a ventilated ceiling of an indoor space. When the heating fluid or the cooling fluid flows thr...
PUM
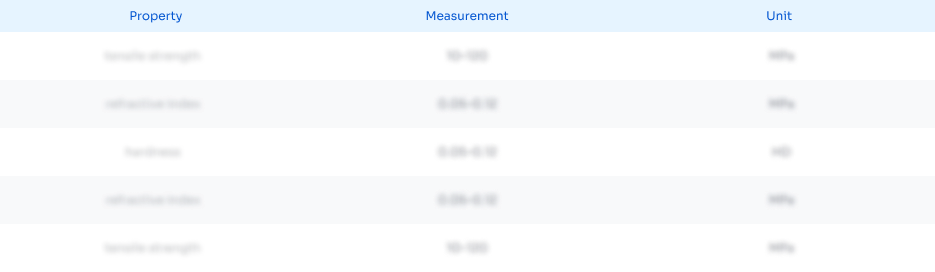
Abstract
Description
Claims
Application Information

- R&D
- Intellectual Property
- Life Sciences
- Materials
- Tech Scout
- Unparalleled Data Quality
- Higher Quality Content
- 60% Fewer Hallucinations
Browse by: Latest US Patents, China's latest patents, Technical Efficacy Thesaurus, Application Domain, Technology Topic, Popular Technical Reports.
© 2025 PatSnap. All rights reserved.Legal|Privacy policy|Modern Slavery Act Transparency Statement|Sitemap|About US| Contact US: help@patsnap.com