Whole tailings depth controllable homogeneous concentration method
A full tailings and depth technology, applied in separation methods, chemical instruments and methods, earth square drilling and mining, etc., can solve problems such as increased energy consumption, complex processes, and inability to meet the needs of mine filling, and achieves low energy consumption and particle size reduction. The effect of uniform grade composition and stable concentration
- Summary
- Abstract
- Description
- Claims
- Application Information
AI Technical Summary
Problems solved by technology
Method used
Image
Examples
Embodiment 1
[0024] Example 1: The concentration of the whole tailings mortar in mineral processing is 10% to 25%. After being concentrated in a CH thickener, the concentration reaches more than 75%.
[0025] When using the CH thickener for the first operation, fill the CH thickener with water first, and stop adding water to the CH thickener after the water flows out from the overflow weir. Then add the whole tailing mortar to the CH thickener, the mortar concentration is 10%~25%, and continuously transport the tailing mortar to the CH thickener. The operator closely monitors the change of the concentration of the underflow mortar, and adjusts according to the change of the concentration at the bottom of the CH thickener. Controllable valves, water supply and underflow circulation, manual control or automatic control, to ensure uniform concentration rise, after 16 hours of settlement, CH thickener underflow concentration reaches 74.5-76.5%, tailing mortar particle size distribution is unifo...
Embodiment 2
[0028] Example 2: Mortar with a thickness of 1 meter is stored in the CH thickener, and the concentration of the whole tailing mortar in the beneficiation is 10% to 25%. After being concentrated in the CH thickener, the concentration reaches more than 75%.
[0029] Continuously add full-tailed mortar to the CH thickener, with a mortar concentration of 10% to 25%, and continuously deliver the tailing mortar to the CH thickener. The operator closely monitors the change in the concentration of the underflow mortar, and adjusts according to the change in the concentration at the bottom of the CH thickener. Controllable valves, water supply and underflow circulation, manual control or automatic control, to ensure a uniform increase in concentration, after the thickness of the slurry in the CH thickener reaches 2.5 meters, the underflow concentration of the CH thickener reaches 74.5-76.5%, and the particle size distribution of the tailing mortar uniform, and to ensure a uniform and c...
PUM
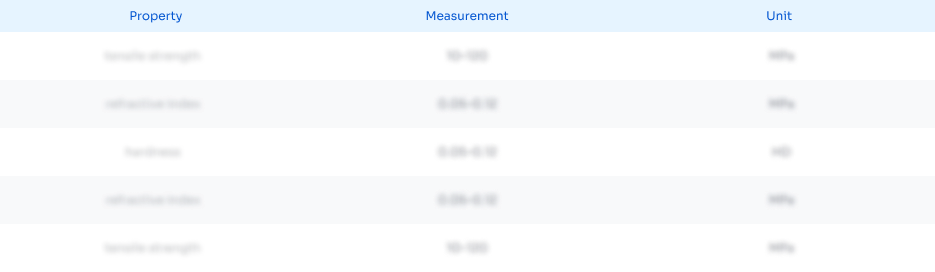
Abstract
Description
Claims
Application Information

- R&D
- Intellectual Property
- Life Sciences
- Materials
- Tech Scout
- Unparalleled Data Quality
- Higher Quality Content
- 60% Fewer Hallucinations
Browse by: Latest US Patents, China's latest patents, Technical Efficacy Thesaurus, Application Domain, Technology Topic, Popular Technical Reports.
© 2025 PatSnap. All rights reserved.Legal|Privacy policy|Modern Slavery Act Transparency Statement|Sitemap|About US| Contact US: help@patsnap.com