Slag mixed active powder concrete
A technology of active powder and concrete, applied in the direction of climate sustainability, sustainable waste treatment, solid waste management, etc., can solve the problem of long-term durability performance cannot be guaranteed, and achieve the effect of reducing the amount of cement
- Summary
- Abstract
- Description
- Claims
- Application Information
AI Technical Summary
Problems solved by technology
Method used
Examples
Embodiment 1
[0030] The weight ratio relative to Portland cement is:
[0032] Silica powder: 0.3 Quartz powder: 0.3
[0033] River Sand: 1.5 Water: 0.25
[0034] Steel fiber: 0.015 Water reducer: 0.025
[0035] Wherein, the content of the steel fiber refers to the ratio of the volume of the steel fiber to the volume of the material after preparation and molding.
[0036] Weigh each component as required, pour cement, river sand, slag, silica powder and quartz powder into the mixing pot, and dry mix for 1 minute. Mix the required water reducer with water, first add half of the water to the stirring pot, and stir for 3 minutes. Add the other half of the water and stir for 3 minutes. Then add half of the amount of steel fiber and stir for 3 minutes, then add the remaining half of the steel fiber and stir for 3 minutes.
[0037] The molding test mold adopts the standard cement mortar triple test mold, and the size is 40mm×40mm×160mm. After the mixture is inj...
Embodiment 2
[0039] The weight ratio relative to Portland cement is:
[0041] Silica powder: 0.3 Quartz powder: 0.3
[0042] River Sand: 1.5 Water: 0.25
[0043] Water reducer: 0.025
[0044] Weigh each component as required, pour cement, river sand, slag, silica powder and quartz powder into the mixing pot, and dry mix for 1 minute. Mix the required water reducer with water, first add half of the water to the stirring pot, and stir for 3 minutes. Add the other half of the water and stir for 3 minutes.
[0045] The molding test mold adopts the standard cement mortar triple test mold, and the size is 40mm×40mm×160mm. After the mixture is injected, vibrate on a shaking table for 180s. After the test piece is formed, put it into the curing box for curing (temperature (20? 1) ℃, humidity > 90%), and remove the mold after 24 hours. Then put them into 90°C water for thermal curing for 3 days. After the thermal curing is completed, wait for it to cool down to ...
Embodiment 3
[0047] The weight ratio relative to Portland cement is:
[0048] Cement: 1 Slag: 0.4
[0049] Silica powder: 0.3 Quartz powder: 0.3
[0050] River Sand: 1.5 Water: 0.25
[0051] Steel fiber: 0.015 Water reducer: 0.03
[0052] Wherein, the content of the steel fiber refers to the ratio of the volume of the steel fiber to the volume of the material after preparation and molding.
[0053] Weigh each component as required, pour cement, river sand, slag, silica powder and quartz powder into the mixing pot, and dry mix for 1 minute. Mix the required water reducer with water, first add half of the water to the stirring pot, and stir for 3 minutes. Add the other half of the water and stir for 3 minutes. Then add half of the amount of steel fiber and stir for 3 minutes, then add the remaining half of the steel fiber and stir for 3 minutes.
[0054]The molding test mold adopts the standard cement mortar triple test mold, and the size is 40mm×40mm×160mm. After the mixture is injec...
PUM
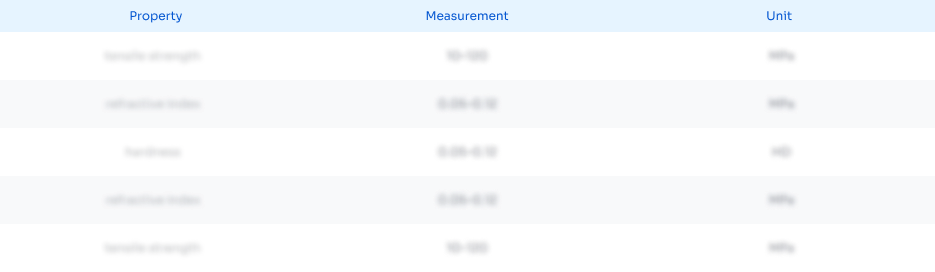
Abstract
Description
Claims
Application Information

- R&D
- Intellectual Property
- Life Sciences
- Materials
- Tech Scout
- Unparalleled Data Quality
- Higher Quality Content
- 60% Fewer Hallucinations
Browse by: Latest US Patents, China's latest patents, Technical Efficacy Thesaurus, Application Domain, Technology Topic, Popular Technical Reports.
© 2025 PatSnap. All rights reserved.Legal|Privacy policy|Modern Slavery Act Transparency Statement|Sitemap|About US| Contact US: help@patsnap.com