Hub manufacturing technology
A technology of manufacturing process and casting process, which is applied in the field of wheel hub manufacturing process, can solve problems such as rising production costs, hidden dangers of wheels being impacted, and danger of wheel hubs, and achieve the effects of simplifying structure and cost, ensuring mechanical properties, and improving overall performance
- Summary
- Abstract
- Description
- Claims
- Application Information
AI Technical Summary
Problems solved by technology
Method used
Image
Examples
Embodiment 1
[0052] As shown in Figures 2 to 8, the hub manufacturing process includes the following steps:
[0053]1. The wheel disc 1 is made by casting technology, and can be manufactured by various traditional methods such as gravity casting, low pressure casting, liquid squeeze casting or other pressure field casting. The casting of this part is because the height of the wheel disc 1 is higher than that of the entire wheel hub. There is no rear rim part, so the height is much lower, which greatly reduces the difficulty of the process and improves the production efficiency. At the same time, this casting can be completed only by the upper mold 2 and the lower mold 3, without the need for side molds, as shown in Figure 2 , while greatly reducing the cost of the mold, it is also possible to carry out the material removal process on the part 4 that is prone to casting hot joints, as shown in Figure 3, so as to fundamentally solve the casting hot joint problem of the casting wheel 1. The w...
Embodiment 2
[0061] As shown in Figure 9, Figure 9 is a three-piece hub produced using this hub manufacturing process. The two rims 6 and the wheel disc 1 in the figure are welded by friction stir welding, and the manufacturing process is similar to that of Embodiment 1.
PUM
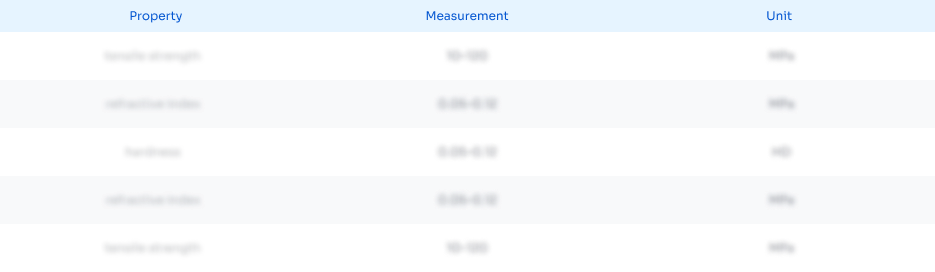
Abstract
Description
Claims
Application Information

- R&D
- Intellectual Property
- Life Sciences
- Materials
- Tech Scout
- Unparalleled Data Quality
- Higher Quality Content
- 60% Fewer Hallucinations
Browse by: Latest US Patents, China's latest patents, Technical Efficacy Thesaurus, Application Domain, Technology Topic, Popular Technical Reports.
© 2025 PatSnap. All rights reserved.Legal|Privacy policy|Modern Slavery Act Transparency Statement|Sitemap|About US| Contact US: help@patsnap.com