Precision shaping molds separating group processing method
A technology of precision molding, disassembly and combination, applied in the direction of casting mold composition, casting molding equipment, metal processing equipment, etc., can solve the problems of failing to meet product design requirements, inaccurate sliding positioning, splashing of high-temperature liquid, etc., and achieve low cost , easy processing, and fully qualified effect
- Summary
- Abstract
- Description
- Claims
- Application Information
AI Technical Summary
Problems solved by technology
Method used
Image
Examples
Embodiment Construction
[0012] In Figure 1, when the six parts of the moving core 5 are reassembled, they are in a loose state and cannot be positioned correctly. When assembling, it is necessary to check the degree of bonding at the joint surface A of the two adjacent cores to ensure that the surface and surface Between more than 90% closeness;
[0013] In Figure 2, fix the moving model core 5 with hoop 2 and six M12 fastening screws 1, adjust the position of the M12 fastening screws 1, and try to ensure that the force is even, so that the radial position of the moving model core 5 is roughly consistent, and the moving model After the core 5 is fixed, it is clamped on a lathe, and the small-end positioning device 3 and the large-end positioning device 4 are processed. At this time, under the action of the small-end positioning device 3 and the large-end positioning device 4, the moving model core 5 is locked. When the hoop 2 is taken off, each component of the moving model core 5 can be firmly conne...
PUM
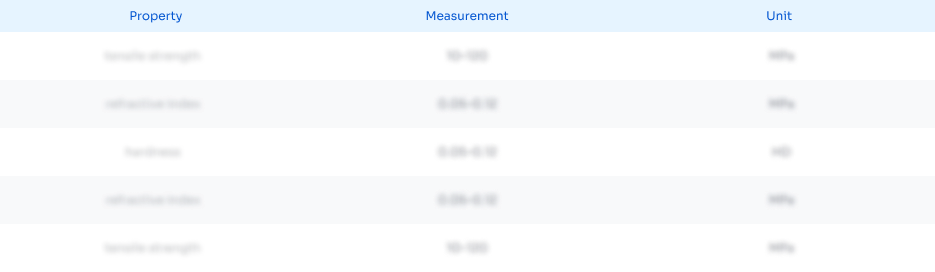
Abstract
Description
Claims
Application Information

- R&D
- Intellectual Property
- Life Sciences
- Materials
- Tech Scout
- Unparalleled Data Quality
- Higher Quality Content
- 60% Fewer Hallucinations
Browse by: Latest US Patents, China's latest patents, Technical Efficacy Thesaurus, Application Domain, Technology Topic, Popular Technical Reports.
© 2025 PatSnap. All rights reserved.Legal|Privacy policy|Modern Slavery Act Transparency Statement|Sitemap|About US| Contact US: help@patsnap.com