Method for preparing chitosan complex film using glycerin and stearic acid as plasticizer
A technology of chitosan and plasticizer, which is applied in the field of preparation of chitosan composite films, can solve the problems of low water permeability and air permeability, increase air permeability, reduce toughness and the like, and achieve the effect of low water permeability and air permeability.
- Summary
- Abstract
- Description
- Claims
- Application Information
AI Technical Summary
Problems solved by technology
Method used
Examples
Embodiment 1
[0019] Weigh 1 g of chitosan and dissolve it in 100 mL of 1% acetic acid solution by volume, add 0.2 ml of glycerin and 0.6 g of stearic acid, heat in a water bath at 70°C until completely dissolved, and cool to room temperature to form a film solution. Filter the above-prepared membrane solution with gauze to remove impurities, and pump it under a vacuum of 0.1MPa for 0.5h, then take 50ml of the solution and pour it evenly on a glass plate, and dry it in a constant temperature drying oven at 40°C to form a film. After the film was removed, the film was carefully peeled off with a clean blade to obtain a chitosan composite film.
Embodiment 2
[0021] Weigh 1.25g of chitosan and dissolve it in 100mL of 1.5% acetic acid solution by volume ratio, add 0.4ml of glycerin and 0.4g of stearic acid, heat in a water bath at 70°C until completely dissolved, cool to room temperature, and form a film solution . Filter the above-prepared membrane solution with gauze to remove impurities, and pump it under a vacuum of 0.1MPa for 0.5h, then take 50ml of the solution and pour it evenly on a glass plate, and dry it in a constant temperature drying oven at 60°C to form a film. After the film was removed, the film was carefully peeled off with a clean blade to obtain a chitosan composite film.
Embodiment 3
[0023] Weigh 1.5g of chitosan and dissolve it in 100mL of 1% acetic acid solution by volume ratio, add 0.4ml of glycerin and 0.5g of stearic acid, heat in a water bath at 70°C until completely dissolved, cool to room temperature, and make a film solution . Filter the above-prepared membrane solution with gauze to remove impurities, and pump it under a vacuum of 0.1MPa for 0.5h, then take 50ml of the solution and pour it evenly on a glass plate, and dry it in a constant temperature drying oven at 60°C to form a film. After the film was removed, the film was carefully peeled off with a clean blade to obtain a chitosan composite film.
PUM
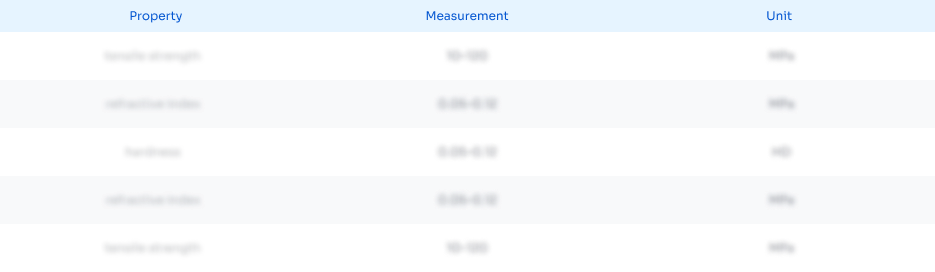
Abstract
Description
Claims
Application Information

- Generate Ideas
- Intellectual Property
- Life Sciences
- Materials
- Tech Scout
- Unparalleled Data Quality
- Higher Quality Content
- 60% Fewer Hallucinations
Browse by: Latest US Patents, China's latest patents, Technical Efficacy Thesaurus, Application Domain, Technology Topic, Popular Technical Reports.
© 2025 PatSnap. All rights reserved.Legal|Privacy policy|Modern Slavery Act Transparency Statement|Sitemap|About US| Contact US: help@patsnap.com