High carbonyl content oxidation starch and method for making same
A technology of oxidized starch and high carbonyl groups, which is applied in the field of oxidized starch and its preparation, can solve the problems of restricting the wide application of oxidized starch, low degree of oxidation of the product, complicated preparation method, etc., and achieve reduced preparation cost, simple process, and favorable processing and molding Effect
- Summary
- Abstract
- Description
- Claims
- Application Information
AI Technical Summary
Problems solved by technology
Method used
Image
Examples
Embodiment 1
[0027] Weigh the dried cornstarch with water to make a starch emulsion with a concentration of 25%, then heat up to 70°C and stir for gelatinization for 0.5 hours, then cool to room temperature, add 150 parts of water and stir evenly; 0.2 hydrogen peroxide was slowly added dropwise, and stirred and reacted at a temperature of 35°C for 6 hours; 200 parts of water was added to the reaction product and stirred evenly, and the supernatant liquid was poured off after standing for stratification, and the emulsion was centrifuged to separate the obtained solid first. Vacuum dry at 35°C for 48 hours, and then dry at 95°C for 12 hours to obtain oxidized starch. Its carbonyl content was measured to be 30.2%, and the yield was 87.1%.
Embodiment 2
[0029]Weigh the dried cornstarch with water to make a starch emulsion with a concentration of 20%, then heat up to 80°C and stir for gelatinization for 1 hour, then cool to room temperature, add 120 parts of water and stir evenly; 3.1 Hydrogen peroxide was slowly added dropwise, and stirred and reacted at a temperature of 15°C for 36 hours; 200 parts of water was added to the reaction product and stirred evenly, and the supernatant liquid was poured out after standing for stratification, and the emulsion was centrifuged to separate the obtained solid first. Vacuum dry at 50°C for 12 hours, and then dry at 95°C for 12 hours to obtain oxidized starch. Its carbonyl content was measured to be 38.5%, and the yield was 83.3%.
Embodiment 3
[0031] Weigh dry cornstarch with water to make a starch emulsion with a concentration of 30%, then raise the temperature to 85°C, stir and gelatinize for 2 hours, cool to room temperature, and then add 120 parts of water to it and stir evenly; 0.5 hydrogen peroxide was slowly added dropwise, stirred and reacted at a temperature of 50°C for 12 hours; 200 parts of water was added to the reaction product and stirred evenly, and the supernatant liquid was poured out after standing for stratification, and the emulsion was centrifuged to obtain a solid First vacuum-dry at 60°C for 12 hours, then dry at 95°C for 12 hours to obtain oxidized starch. Its carbonyl content was measured to be 55.4%, and the yield was 88.5%.
PUM
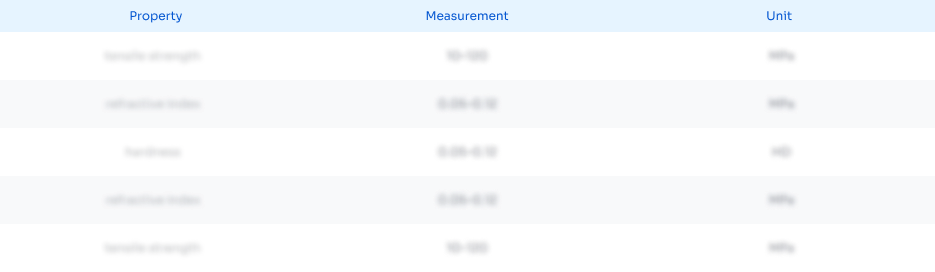
Abstract
Description
Claims
Application Information

- Generate Ideas
- Intellectual Property
- Life Sciences
- Materials
- Tech Scout
- Unparalleled Data Quality
- Higher Quality Content
- 60% Fewer Hallucinations
Browse by: Latest US Patents, China's latest patents, Technical Efficacy Thesaurus, Application Domain, Technology Topic, Popular Technical Reports.
© 2025 PatSnap. All rights reserved.Legal|Privacy policy|Modern Slavery Act Transparency Statement|Sitemap|About US| Contact US: help@patsnap.com