Method for producing bubble aluminum alloy special-shaped member with even pore structure
A foamed aluminum alloy and uniform pore technology is applied in the field of preparing foamed aluminum alloy special-shaped parts with uniform pore structure, which can solve the problems of large outgassing, concentrated shrinkage cavities, and difficulty in uniform porosity, and achieves simplified process, uniform pore structure, simple method effect
- Summary
- Abstract
- Description
- Claims
- Application Information
AI Technical Summary
Problems solved by technology
Method used
Image
Examples
Embodiment 1
[0021]A method for preparing aluminum alloy special-shaped parts with a uniform pore structure, comprising the following steps: the first step: heating the aluminum alloy to melt, wherein the aluminum alloy such as ZL101, ZL102, ZL111 series alloys can also be cast aluminum Copper-based alloys, grades such as ZL201, ZL202, ZL205 series alloys, or deformed aluminum alloys mainly containing copper or silicon, or aluminum alloys containing magnesium, such as ZL301, ZL302, etc., and adjust the temperature to 630 ° C -680°C, the temperature can be 635°C, 642°C, 650°C, 660°C, 665°C, 670°C, 675°C, adding titanium hydride equivalent to 0.5%-5% of the weight of the aluminum alloy, the amount of titanium hydride can be Select 0.8%, 1.2%, 1.5%, 2.0%, 2.8%, 3.5%, 4.2%, 4.7%, stir at a speed of 500-800rpm for 60-500 seconds to disperse titanium hydride, for example, it can be selected as 500rpm, 600rpm, 700rpm, 750rpm, the stirring time can be selected as: 70s, 90s, 150s, 250s, 400s, 550s,...
Embodiment 2
[0024] A method for preparing aluminum alloy special-shaped parts with a uniform pore structure, comprising the following steps: the first step: heating the aluminum alloy to melt, wherein the aluminum alloy such as ZL101, ZL102, ZL111 series alloys can also be cast aluminum Copper-based alloys, grades such as ZL201, ZL202, ZL205 series alloys, or deformed aluminum alloys mainly containing copper or silicon, or aluminum alloys containing magnesium, such as ZL301, ZL302, etc., and adjust the temperature to 630 ° C -680°C, the temperature can be 635°C, 642°C, 650°C, 660°C, 665°C, 670°C, 675°C, adding titanium hydride equivalent to 0.5%-5% of the weight of the aluminum alloy, the amount of titanium hydride can be Select 0.8%, 1.2%, 1.5%, 2.0%, 2.8%, 3.5%, 4.2%, 4.7%, stir at a speed of 500-800rpm for 60-500 seconds to disperse titanium hydride, for example, it can be selected as 500rpm, 600rpm, 700rpm, 750rpm, the stirring time can be selected as: 70s, 90s, 150s, 250s, 400s, 550s...
PUM
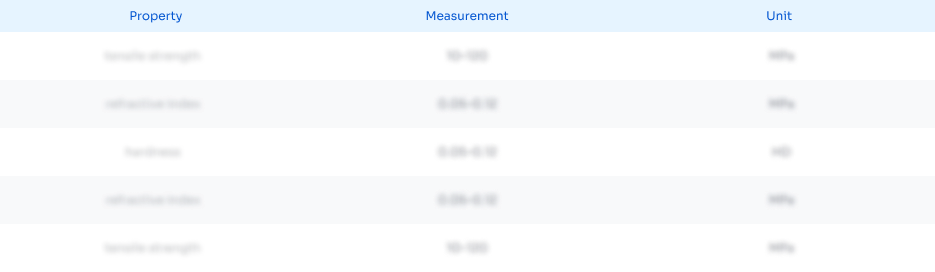
Abstract
Description
Claims
Application Information

- R&D
- Intellectual Property
- Life Sciences
- Materials
- Tech Scout
- Unparalleled Data Quality
- Higher Quality Content
- 60% Fewer Hallucinations
Browse by: Latest US Patents, China's latest patents, Technical Efficacy Thesaurus, Application Domain, Technology Topic, Popular Technical Reports.
© 2025 PatSnap. All rights reserved.Legal|Privacy policy|Modern Slavery Act Transparency Statement|Sitemap|About US| Contact US: help@patsnap.com