Cement disperser and its preparing method
A technology of cement dispersant and general formula, which is applied in the field of polycarboxylate polymer cement dispersant and its preparation, and can solve the problem of large excess, large slump loss of polycarboxylate water reducer over time, reduction of water reducer Insufficient water performance and other problems, achieve low viscosity, low water-cement ratio, and improve workability
- Summary
- Abstract
- Description
- Claims
- Application Information
AI Technical Summary
Problems solved by technology
Method used
Image
Examples
Embodiment 1
[0028] In a four-necked flask equipped with stirring, thermometer, ventilation device and dropping device, add 140 parts of deionized water and 30 parts of sodium methallyl sulfonate, and heat up to 60 ° C under stirring and nitrogen filling conditions, while Add dropwise the mixed aqueous solution that is made up of 40 parts of polyoxyethylene base monomethyl ether methacrylate, 30 parts of acrylic acid, 1 part of 3-mercaptopropionic acid and 10 grams of 5% ammonium persulfate aqueous solution, and the dropping time is controlled at 30min. After the dropwise addition, keep the temperature at 60° C. for 4 hours to complete the reaction. After the reaction, use 55 parts by weight of 30% sodium hydroxide solution to neutralize the pH value of the solution to about 7.0 to obtain cement dispersant sample 1. The test results are shown in Table 1.
Embodiment 2
[0030] In a four-necked flask equipped with stirring, thermometer, ventilation device and dropping device, add 17 parts of deionized water and 5 parts of sodium methallyl sulfonate, and raise the temperature to 70 ° C under stirring and nitrogen filling conditions, while Add dropwise the mixed aqueous solution that is made up of 90 parts of polyoxyethylene base monomethyl ether methacrylate, 30 parts of acrylic acid, 0.625 part of 3-mercaptopropionic acid and 20 grams of 5% ammonium persulfate aqueous solution, and the dropping time is controlled at 40min. After the dropwise addition, keep the temperature at 70°C for 3 hours to complete the reaction. After the reaction, neutralize the pH value of the solution to about 7.0 with 55 parts of 30% potassium hydroxide solution to obtain cement dispersant sample 2. The test results are shown in Table 1.
Embodiment 3
[0032] In a four-necked flask equipped with stirring, thermometer, ventilation device and dropping device, add 66 parts of deionized water and 5 parts of sodium methallyl sulfonate, and raise the temperature to 80 ° C under stirring and nitrogen filling conditions, while A mixed aqueous solution composed of 40 parts of polyoxyethylene monomethyl ether methacrylate, 55 parts of acrylic acid, 0.1 part of 3-mercaptopropionic acid and 40 parts of 5% ammonium persulfate aqueous solution was added dropwise, and the dropping time was controlled at 50min. After the dropwise addition, keep the temperature at 80°C for 2 hours to complete the reaction. After the reaction, use 101 parts of 30% ammonium hydroxide solution to neutralize the pH value of the solution to about 7.0 to obtain cement dispersant sample 3. The test results are shown in Table 1.
PUM
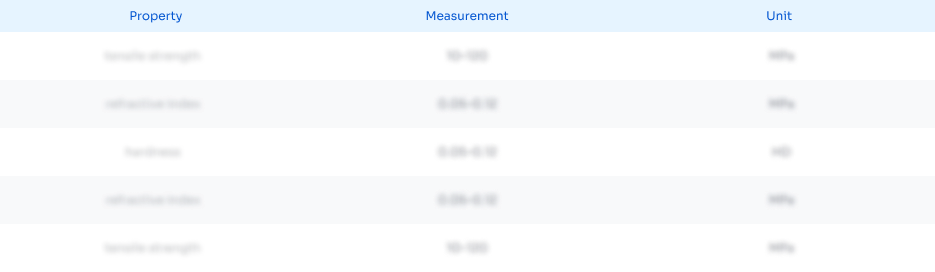
Abstract
Description
Claims
Application Information

- R&D Engineer
- R&D Manager
- IP Professional
- Industry Leading Data Capabilities
- Powerful AI technology
- Patent DNA Extraction
Browse by: Latest US Patents, China's latest patents, Technical Efficacy Thesaurus, Application Domain, Technology Topic, Popular Technical Reports.
© 2024 PatSnap. All rights reserved.Legal|Privacy policy|Modern Slavery Act Transparency Statement|Sitemap|About US| Contact US: help@patsnap.com