Obstruct explosion-proof material and manufacturing technique thereof
A technology that blocks explosion-proof materials and manufacturing processes. It is applied in metal rolling, gas/liquid distribution and storage, and internal accessories. It can solve problems such as cracking, debris, and oil circuit blockage.
- Summary
- Abstract
- Description
- Claims
- Application Information
AI Technical Summary
Problems solved by technology
Method used
Image
Examples
Embodiment 1
[0013] A barrier and explosion-proof material, made of slit and expanded aluminum alloy foil mesh, with a honeycomb porous structure, the chemical composition weight percentage of aluminum alloy foil is: silicon 0.55%, iron 0.65%, copper 0.13%, manganese 1.3%, zinc 0.1%, titanium 0.15%, aluminum as the balance.
[0014] The manufacturing process steps of the above-mentioned barrier and explosion-proof materials are: rolling the aluminum alloy ingot containing the above-mentioned chemical composition into aluminum alloy foil, cutting it into slit aluminum foil by a slitting machine, then shaping and winding, and then rolling the shaped and rolled aluminum foil. The aluminum foil is tempered, the tempering temperature is 220°C, and the tempering time is 10 hours. The tempered aluminum foil is discharged and slitting and rolling, and then the expanded mesh is expanded into an aluminum foil mesh, and the aluminum foil mesh is stacked. Formed into a mesh barrier explosion-proof mat...
Embodiment 2
[0016] A barrier explosion-proof material, made of slit and expanded aluminum alloy foil mesh, with a honeycomb porous structure, the chemical composition weight percentage of aluminum alloy foil is: silicon 0.4%, iron 0.45%, copper 0.15%, manganese 0.8%, zinc 0.1%, titanium 0.1%, aluminum as the balance.
[0017] The manufacturing process steps of the above-mentioned barrier and explosion-proof materials are: rolling the aluminum alloy ingot containing the above-mentioned chemical composition into aluminum alloy foil, cutting it into slit aluminum foil by a slitting machine, then shaping and winding, and then rolling the shaped and rolled aluminum foil. The aluminum foil is tempered, the tempering temperature is 240°C, and the tempering time is 8 hours. The tempered aluminum foil is discharged and slit and rolled, and then the expanded mesh is expanded into an aluminum foil mesh, and the aluminum foil mesh is stacked to form a The type is a mesh barrier explosion-proof materi...
Embodiment 3
[0019] A barrier and explosion-proof material, made of slit and expanded aluminum alloy foil mesh, with a honeycomb porous structure, the chemical composition weight percentage of aluminum alloy foil is: silicon 0.6%, iron 0.3%, copper 0.2%, manganese 1.0%, zinc 0.1%, titanium 0.2%, aluminum as the balance.
[0020] The manufacturing process steps of the above-mentioned barrier and explosion-proof materials are: rolling the aluminum alloy ingot containing the above-mentioned chemical composition into aluminum alloy foil, cutting it into slit aluminum foil by a slitting machine, then shaping and winding, and then rolling the shaped and rolled aluminum foil. The aluminum foil is tempered, the tempering temperature is 230°C, and the tempering time is 9 hours. The tempered aluminum foil is discharged and slit and rolled, and then the expanded mesh is expanded into an aluminum foil mesh, and the aluminum foil mesh is stacked to form a The type is a mesh barrier explosion-proof mate...
PUM
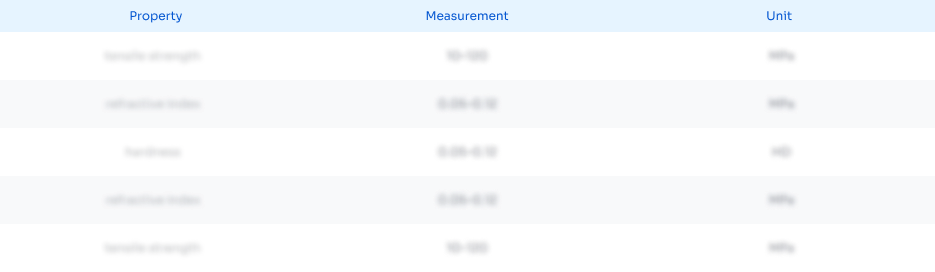
Abstract
Description
Claims
Application Information

- Generate Ideas
- Intellectual Property
- Life Sciences
- Materials
- Tech Scout
- Unparalleled Data Quality
- Higher Quality Content
- 60% Fewer Hallucinations
Browse by: Latest US Patents, China's latest patents, Technical Efficacy Thesaurus, Application Domain, Technology Topic, Popular Technical Reports.
© 2025 PatSnap. All rights reserved.Legal|Privacy policy|Modern Slavery Act Transparency Statement|Sitemap|About US| Contact US: help@patsnap.com