High grade cold rolling non-oriented silicon steel and method for manufacturing same
A technology of oriented silicon steel and manufacturing method, applied in metal rolling, manufacturing tools, metal rolling and other directions, can solve the problems of high production equipment requirements, high production process control precision requirements, complex procedures, etc., to achieve equipment and process aspects. The requirements are not high, the surface corrugated defects are eliminated, and the process versatility is strong.
- Summary
- Abstract
- Description
- Claims
- Application Information
AI Technical Summary
Problems solved by technology
Method used
Image
Examples
Embodiment 1
[0064] The converter and RH vacuum treatment obtain C: 0.0028%, Si: 1.65%, Mn: 0.95%, Al: 0.28%, P: 0.015%, S: 0.0035%, N: 0.0035%, and the rest is molten steel with Fe at 0.9m / min continuous casting into a slab with a thickness of 200mm. The slab is soaked at 1120°C. The rough rolling adopts 5 passes. After 20%→25%→28%→32%→27% reduction Lower rate / pass, finishing temperature of finishing rolling is 820℃, coiling temperature is 620℃, thickness of hot-rolled plate is 2.0mm, after pickling, cold-rolled to thickness of 0.5mm by one-time method, cold-rolled steel strip is recrystallized. The annealing atmosphere adopts a dry atmosphere and does not need to be humidified and decarburized. There is no corrugated defect> 2μm in the finished steel plate, and the magnetism is P 15 / 50 =3.46W / kg, B 50 = 1.703T.
[0065] The composition (weight percentage) of the medium-to-high grade cold-rolled non-oriented silicon steel made in this embodiment is: C: 0.0028%, Si: 1.65%, Mn: 0.95%, Al: 0.28...
Embodiment 2
[0067] The converter and RH vacuum treatment obtain C: 0.003%, Si: 1.75%, Mn: 1.20%, Al: 0.38%, P: 0.013%, S: 0.0032%, N: 0.0030%, and the rest is molten steel with Fe at 0.85m / min continuous casting into a slab with a thickness of 210mm, the slab is hot rolled at 1130℃, and the rough rolling adopts 5 passes. After 23%→25%→28%→32%→27% reduction Lower rate / pass, finishing temperature of finishing rolling is 840℃, coiling temperature is 630℃, thickness of hot-rolled plate is 2.4mm, after pickling, cold-rolled to thickness of 0.5mm by one-time method, cold-rolled steel strip is recrystallized. Annealing, the annealing atmosphere is a dry atmosphere, and no humidification and decarburization treatment is required. There is no corrugated defect of height> 2μm in the finished board, and the magnetic properties are P15 / 50=3.24W / kg, B50=1.689T.
[0068] The composition (weight percentage) of the medium-to-high grade cold-rolled non-oriented silicon steel produced in this embodiment is: C...
Embodiment 3
[0070] Converter and RH vacuum treatment yield C: 0.003%, Si: 1.75%, Mn: 1.20%, Al: 0.38%, P: 0.013%, S: 0.0032%, N: 0.0030%, Sn: 0.05%, Sb: 0.08% , Cu: 0.02%, the rest is Fe molten steel, is continuously cast into a slab with a thickness of 210mm at a drawing speed of 0.85m / min. The slab is hot-rolled at 1130℃, and the rough rolling adopts 5 passes. 23%, 25%, 28%, 32%, 27% reduction rate / pass, finishing temperature of finishing rolling is 843℃, coiling temperature is 635℃, thickness of hot-rolled plate is 2.4mm, after pickling, use one-time cooling The cold-rolled steel strip is rolled to a thickness of 0.5mm, and the finished product is recrystallized and annealed. The annealing atmosphere is a dry atmosphere and does not require humidification and decarburization. There is no corrugated defect with a height of >2μm in the finished board, and the magnetic properties are P15 / 50=3.26W / kg and B50=1.698T.
[0071] The composition (weight percentage) of the medium-to-high grade cold-...
PUM
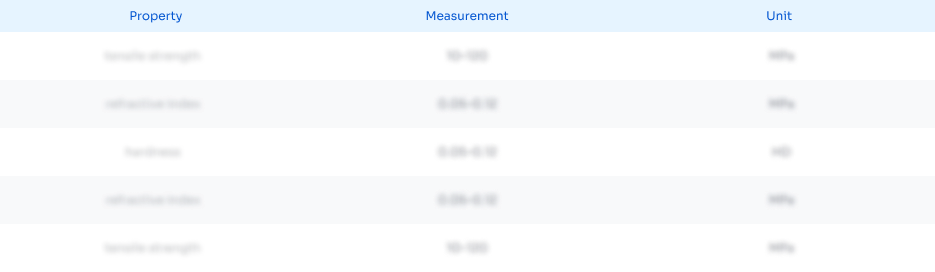
Abstract
Description
Claims
Application Information

- Generate Ideas
- Intellectual Property
- Life Sciences
- Materials
- Tech Scout
- Unparalleled Data Quality
- Higher Quality Content
- 60% Fewer Hallucinations
Browse by: Latest US Patents, China's latest patents, Technical Efficacy Thesaurus, Application Domain, Technology Topic, Popular Technical Reports.
© 2025 PatSnap. All rights reserved.Legal|Privacy policy|Modern Slavery Act Transparency Statement|Sitemap|About US| Contact US: help@patsnap.com