Rocker bearing high carbon-chrome steel outer ring composite treatment technology
A composite treatment, high-carbon chromium steel technology, applied in the direction of bearing components, shafts and bearings, engine components, etc., can solve problems such as bearing wear and crack failure, engine failure, etc.
- Summary
- Abstract
- Description
- Claims
- Application Information
AI Technical Summary
Problems solved by technology
Method used
Examples
Embodiment Construction
[0005] Take a bearing ring (high-carbon chromium steel GCr15) with an outer diameter of 25mm, an inner diameter of 19mm, and a width of 12mm as an example. First, heat-treat the bearing ring of the rocker arm in a box-type multipurpose furnace. 3.5 hours, while the carbon potential in the heating furnace atmosphere is kept at 1.05 and the nitrogen potential volume ratio is 5% (the gas volume ratio in the furnace). After heat preservation, it is cooled and quenched in quenching oil. The ferrule after rough grinding is put into the shot blasting machine, and the ceramic shot with a diameter of 3.5mm is freely sprayed at a speed of 70m / s for 20 minutes to obtain a large surface compressive stress on the surface.
[0006] After adopting this heat treatment process and rough grinding and shot peening, the amount of residual austenite on the surface of the bearing is 15% to 20%, and the residual compressive stress on the surface is 400 to 1000Mpa.
[0007] After testing and testing,...
PUM
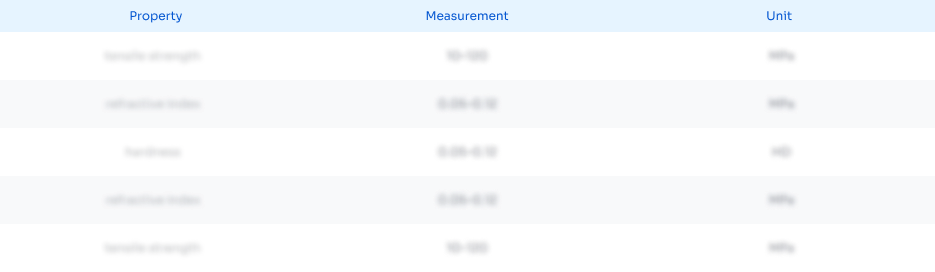
Abstract
Description
Claims
Application Information

- Generate Ideas
- Intellectual Property
- Life Sciences
- Materials
- Tech Scout
- Unparalleled Data Quality
- Higher Quality Content
- 60% Fewer Hallucinations
Browse by: Latest US Patents, China's latest patents, Technical Efficacy Thesaurus, Application Domain, Technology Topic, Popular Technical Reports.
© 2025 PatSnap. All rights reserved.Legal|Privacy policy|Modern Slavery Act Transparency Statement|Sitemap|About US| Contact US: help@patsnap.com