Method for improving solid content of catalytic cracking catalyst slurry
A catalyst slurry and catalytic cracking technology, which is applied in catalytic cracking, physical/chemical process catalysts, chemical instruments and methods, etc. It can solve the problems of destroying molecular sieves, deterioration of catalyst anti-wear strength, and difficulty in pseudo-boehmite
- Summary
- Abstract
- Description
- Claims
- Application Information
AI Technical Summary
Problems solved by technology
Method used
Examples
Embodiment 1
[0042] Add deionized water, 2174 grams of aluminum sol and 2078 grams of kaolin in the reaction kettle, add 200 grams of concentration after beating and be 35% hydrochloric acid, mix well and add 1656 grams of 1 hour under stirring # Pseudo-boehmite, after stirring for 30 minutes, add 1937 grams of REUSY molecular sieves, 123 grams of Fudan ZSM-5 molecular sieves and deionized water mixed molecular sieve slurry, spray dry after beating, and roast the obtained catalyst microspheres at 500 ° C for 0.5 hours, Then add deionized water, stir evenly, wash at 80° C. for 15 minutes, and filter and dry to obtain the FCC catalyst prepared by the method of the present invention, which is recorded as A1.
[0043] The solid content of the spray slurry of catalyst A1 is 39.2w%, the viscosity of the slurry is 4058 centipoise, the wear index of the obtained catalyst is 1.5, and the pore volume is 0.40mL·g -1 , Microreaction Activity 79 .
Embodiment 2
[0052] Add deionized water in the reaction kettle, 2634 grams of aluminum sol and 195 grams of concentration are 35% hydrochloric acid, add 1524 grams of 1# pseudo-boehmite under stirring after mixing, add 1896 grams of kaolin after stirring for 0.5 hours, After beating evenly, add a mixed slurry composed of 2060 grams of REUSY molecular sieves and deionized water, spray dry after beating, and roast the obtained catalyst microspheres at 500°C for 0.5 hours, then add deionized water, stir evenly, and wash at 80°C for 15 minutes, filter and dry to obtain the FCC catalyst prepared by the method of the present invention, which is recorded as A2.
[0053] The solid content of the spray slurry of catalyst A2 is 39.6w%, the viscosity of the slurry is 4856 centipoise, the wear index of the obtained catalyst is 1.7, and the pore volume is 0.41mL·g -1 , micro-reaction activity 80.
Embodiment 3
[0059] Adding 2174 grams of aluminum sol and 200 grams of concentration in the reactor is 35% hydrochloric acid, mix well, then add deionized water and 2078 grams of kaolin, mix well and add 1656 grams of 1 hour under stirring # Pseudo-boehmite, after stirring for 30 minutes, add 1937 grams of REUSY molecular sieves, 123 grams of Fudan ZSM-5 molecular sieves and deionized water mixed molecular sieve slurry, spray dry after beating, and roast the obtained catalyst microspheres at 500 ° C for 0.5 hours, Then add deionized water, stir evenly, wash at 80° C. for 15 minutes, and filter and dry to obtain the FCC catalyst prepared by the method of the present invention, which is recorded as A3.
[0060] The solid content of the spray slurry of catalyst A3 is 39.2w%, the viscosity of the slurry is 4097 centipoise, the wear index of the obtained catalyst is 1.6, and the pore volume is 0.40mL·g -1 , Microreaction Activity 79 .
PUM
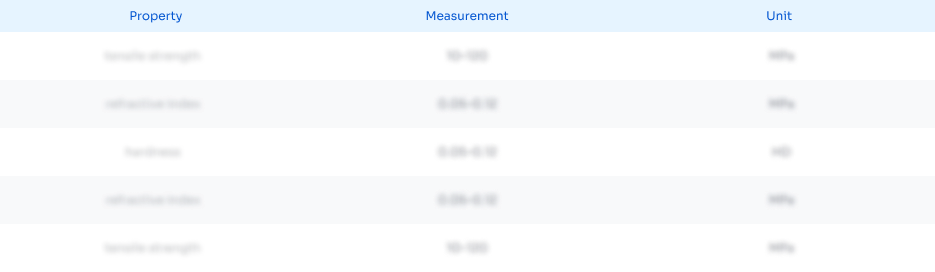
Abstract
Description
Claims
Application Information

- R&D
- Intellectual Property
- Life Sciences
- Materials
- Tech Scout
- Unparalleled Data Quality
- Higher Quality Content
- 60% Fewer Hallucinations
Browse by: Latest US Patents, China's latest patents, Technical Efficacy Thesaurus, Application Domain, Technology Topic, Popular Technical Reports.
© 2025 PatSnap. All rights reserved.Legal|Privacy policy|Modern Slavery Act Transparency Statement|Sitemap|About US| Contact US: help@patsnap.com