Hob complete utilization integrated gear hobbing method
A hobbing method and hob technology, applied in the direction of gear teeth, elements with teeth, belts/chains/gears, etc., can solve the problems of low hob utilization, increased hob axial movement, and short service life. , to achieve the effect of improving work stability and accuracy, overcoming tooth profile errors, and improving service life
- Summary
- Abstract
- Description
- Claims
- Application Information
AI Technical Summary
Problems solved by technology
Method used
Image
Examples
Embodiment
[0049] Processing-normal modulus m n =2mm, number of teeth Z=20, tooth width b=30mm, depth of cut g=4.5 spur gear.
[0050] Hob outer diameter d=100mm, number of hob heads Z0=1
[0051] Processing technology: hob speed n=400 rpm, safety factor k=0.2
[0052] Axial feed f=0.66 mm / rev
[0053] Tangential feed f 1 =0.22mm / rotation
[0054] Radial feed f r =1.2mm / rotation
[0055] Reel Elevation:
[0056]
[0057] Hobbing time:
[0058] = zg nf r z 0 + z ( h + b ) nfz 0 = 20 × 4.5 400 × 1.2 × ...
PUM
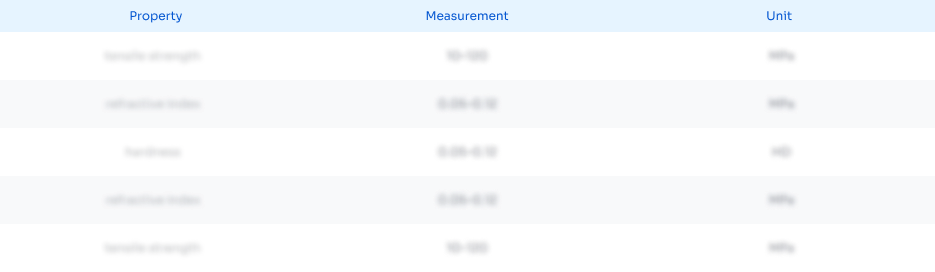
Abstract
Description
Claims
Application Information

- Generate Ideas
- Intellectual Property
- Life Sciences
- Materials
- Tech Scout
- Unparalleled Data Quality
- Higher Quality Content
- 60% Fewer Hallucinations
Browse by: Latest US Patents, China's latest patents, Technical Efficacy Thesaurus, Application Domain, Technology Topic, Popular Technical Reports.
© 2025 PatSnap. All rights reserved.Legal|Privacy policy|Modern Slavery Act Transparency Statement|Sitemap|About US| Contact US: help@patsnap.com