Method for standardizing structural parameter of structure optical vision sensor
A technology of structural parameters and structured light, which is applied to instruments, optical devices, measuring devices, etc., can solve the problems of complicated operation, small number of calibration points, and high cost of processing tooth-shaped targets, and achieves expansion of the scope of application, simple operation, and improved performance. The effect of efficiency
- Summary
- Abstract
- Description
- Claims
- Application Information
AI Technical Summary
Problems solved by technology
Method used
Image
Examples
Embodiment Construction
[0029] The present invention will be further described in detail below in conjunction with the accompanying drawings and specific embodiments.
[0030] Fig. 1 is the overall implementation flowchart of the structural parameter calibration method of the structured light visual sensor of the present invention, as shown in Fig. 1, the calibration method of the present invention includes the following steps:
[0031] Step 11: Establish image plane coordinate system and camera coordinate system. As shown in Figure 2, the camera coordinate system O is established according to the placement position of the camera c -x c the y c z c and the camera image plane coordinate system O-UV.
[0032] Step 12: Establish a target coordinate system, use a camera to capture a planar target image, and perform distortion correction on the captured planar target image. Turn on the power of the laser projector, place a planar target with feature points in the measurement area of the structured ...
PUM
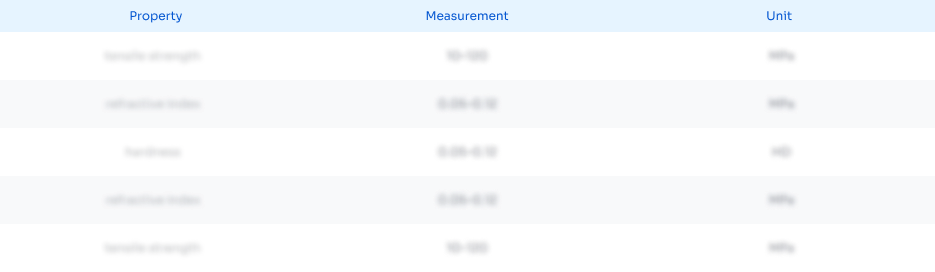
Abstract
Description
Claims
Application Information

- R&D
- Intellectual Property
- Life Sciences
- Materials
- Tech Scout
- Unparalleled Data Quality
- Higher Quality Content
- 60% Fewer Hallucinations
Browse by: Latest US Patents, China's latest patents, Technical Efficacy Thesaurus, Application Domain, Technology Topic, Popular Technical Reports.
© 2025 PatSnap. All rights reserved.Legal|Privacy policy|Modern Slavery Act Transparency Statement|Sitemap|About US| Contact US: help@patsnap.com