Modified propylene ester adhesive and producing method thereof
An adhesive, acrylic technology, applied in the direction of ester copolymer adhesives, adhesive types, etc., can solve the problem of water resistance and bonding strength not up to standard, three waste discharge does not meet environmental protection requirements, poor product feel, etc. problem, to achieve the effect of strong binding force, good use effect, plump and soft hand feeling
- Summary
- Abstract
- Description
- Claims
- Application Information
AI Technical Summary
Problems solved by technology
Method used
Examples
Embodiment 1
[0018] Alkyl methacrylate and vinyl alkanoate obtained by esterification of methacrylic acid and alcohol (alkyl R is C 2 h 5 -), tertiary carbonate, alkenyl alkyl phosphate and deionized water were added sodium persulfate, heated to 78 ~ 82 ℃ to make polymerization reaction, reacted for 4 hours, then added graft monomer acrylic acid and continued to heat to 85 ±2°C, make it polymerize with acrylic acid, react for 6 hours, then keep warm for 1.5 hours, cool down, and then filter the material through 100 mesh to obtain a water-resistant high-strength resin; in vinyl acetate, alkenyl alkyl phosphate , polyvinyl alcohol and deionized water, add sodium persulfate, heat to 68-72°C to cause copolymerization reaction, react for 10 hours, then keep warm at 80-85°C for 1 hour, cool down, and then perform 100-mesh filtration The material is discharged to obtain the base resin; the water-resistant high-strength resin and the base resin are mixed together, and an acid catalyst containing ...
Embodiment 2
[0020] Alkyl acrylate and vinyl alkanoate obtained from the esterification of acrylic acid and alcohol (alkyl R is C 3 h 7 -), acrylate amino ester, ethoxylated phenol ether sulfate and deionized water, add potassium persulfate, heat to 78-82°C to make polymerization reaction, react for 4 hours, then add graft monomer methacrylic acid and Continue heating to 85±2°C to make it polymerize with methacrylic acid for 6 hours, then keep it warm for 1.5 hours, cool down, and then carry out 100-mesh filtration to obtain a water-resistant high-strength resin; Add potassium persulfate to oxyphenol ether sulfate, hydroxyalkyl cellulose and deionized water, heat to 68-72°C to cause copolymerization reaction, react for 10 hours, and then keep warm at 80-85°C for 1 hour , cooling down, and then carry out 100-mesh filtration to obtain the base resin; mix the water-resistant high-strength resin and the base resin together, add an acidic catalyst containing ammonium sulfate at 90-120 ° C, cat...
Embodiment 3
[0022] Alkyl methacrylate and vinyl alkanoate obtained by esterification of methacrylic acid and alcohol (alkyl R is C 3 h 7 -), hydroxy acrylate, alkylphenol polyoxyethylene ether, and deionized water were added ammonium persulfate, heated to 78-82°C to cause polymerization reaction, reacted for 4 hours, and then added graft monomer unsaturated binary acid and continue to heat to 85±2°C to make it polymerize with unsaturated dibasic acid for 6 hours, then keep it warm for 1.5 hours, cool down, and then carry out 100-mesh filtration to obtain water-resistant high-strength resin; Add potassium persulfate to methacrylate monomer, fatty alcohol polyoxyethylene, polyvinyl alcohol, and deionized water, heat to 68-72°C to cause copolymerization reaction, react for 10 hours, and then heat at 80-85°C Keep warm for 1 hour, cool down, and then carry out 100-mesh filtration to obtain the base resin; mix the water-resistant high-strength resin and the base resin together, add an acid cat...
PUM
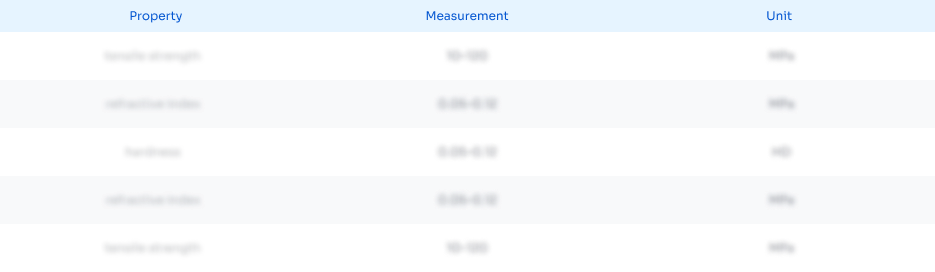
Abstract
Description
Claims
Application Information

- Generate Ideas
- Intellectual Property
- Life Sciences
- Materials
- Tech Scout
- Unparalleled Data Quality
- Higher Quality Content
- 60% Fewer Hallucinations
Browse by: Latest US Patents, China's latest patents, Technical Efficacy Thesaurus, Application Domain, Technology Topic, Popular Technical Reports.
© 2025 PatSnap. All rights reserved.Legal|Privacy policy|Modern Slavery Act Transparency Statement|Sitemap|About US| Contact US: help@patsnap.com