Forming method of current divider
A technology of shunts and resistors, applied in the field of shunts, can solve the problems of low degree of mechanization and automation, high requirements for metal connection, large equipment investment, etc., and achieve saving of material resources and foreign exchange, high and smooth weld quality, and flexible structural design Effect
- Summary
- Abstract
- Description
- Claims
- Application Information
AI Technical Summary
Problems solved by technology
Method used
Image
Examples
Embodiment Construction
[0010] In Fig. 1, the shunt of the present invention is composed of two pieces of red copper 1 and 2 and a piece of manganese copper 3, and the opposite side end faces of the manganin sheet 3 are respectively connected with the side end faces of the two pieces of red copper 1 and 2 , the connection is welding, and there are fixed holes and sampling ends on the copper sheets 1 and 2. The specific forming method is as follows 1. Manganese copper sheet 1, 2 and manganese copper sheet 3 are made. Two 1mm thick red copper sheets 1 and 2 are punched into a rectangle. The length is 1000mm and punched into one piece; first put the above-mentioned copper sheet 1 and a piece of manganese-copper sheet 3 into a high-power laser welding machine for welding, and pass nitrogen gas during welding to prevent the oxidation of the copper sheets 1 and 2 and the manganese-copper sheet being welded. In the same way, the other side of the copper sheet 2 and the manganese-copper sheet 3 is welded; th...
PUM
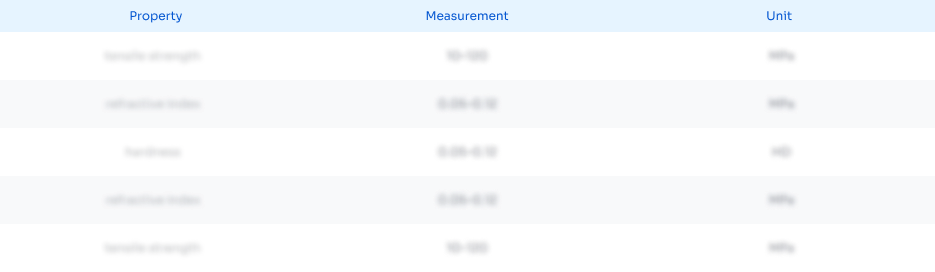
Abstract
Description
Claims
Application Information

- R&D
- Intellectual Property
- Life Sciences
- Materials
- Tech Scout
- Unparalleled Data Quality
- Higher Quality Content
- 60% Fewer Hallucinations
Browse by: Latest US Patents, China's latest patents, Technical Efficacy Thesaurus, Application Domain, Technology Topic, Popular Technical Reports.
© 2025 PatSnap. All rights reserved.Legal|Privacy policy|Modern Slavery Act Transparency Statement|Sitemap|About US| Contact US: help@patsnap.com