High efficiency multifunctional membrane and filter plate with long service life, and forming method
A long-life and high-efficiency technology, applied in chemical instruments and methods, separation methods, filtration and separation, etc., can solve problems such as short service life, affecting product quality, and rupture of diaphragm filter plates, to ensure reliability and stability, The structure method is novel and the effect of realizing the precision
- Summary
- Abstract
- Description
- Claims
- Application Information
AI Technical Summary
Problems solved by technology
Method used
Image
Examples
Embodiment 1
[0045] Embodiment 1: with reference to accompanying drawing 1~14. High-efficiency and long-life multi-functional diaphragm and filter plate, which includes a filter plate core 1 and a diaphragm 2, the diaphragm 2 located on the filter plate core 1 is directly injection-molded on the filter plate core 1 using molds and injection molding equipment, and the shape of the diaphragm 2 is similar to that of the filter plate core. The shapes of the opposite filter plate cores 1 are corresponding. Filter plate core 1 refers to plastic plate core, metal plate core, adjustable temperature plate core, embedded plate core, non-embedded plate core; diaphragm 2 is embedded diaphragm, non-embedded diaphragm. Non-embedded diaphragms refer to flat, semi-enclosed, and all-inclusive diaphragms. The diaphragm is in the form of a unilateral diaphragm or a bilateral diaphragm. The thickness of the diaphragm depends on the thickness of the mold cavity or the injection molding process, which is a pr...
Embodiment 2
[0052] Embodiment 2: On the basis of Embodiment 1, the periphery or all surfaces of one or both surfaces of the filter plate core 1 are directly injected with the diaphragm 2 . The periphery refers to: the periphery of the core surface of the filter plate; the periphery of the side surface of the filter plate core; the combination of the periphery of the core surface of the filter plate and the periphery of the side surface of the filter plate core. All faces refer to all faces of the filter plate core and include inserts in the filter plate core, such as inlet and outlet fluid channels, etc.
Embodiment 3
[0053] Embodiment 3: On the basis of Embodiments 1 and 2, a diaphragm 2 and a filter plate core 1 form a tympanic membrane compressing chamber 3, and both the diaphragm 2 and the filter plate core 1 are made of thermoplastic materials.
PUM
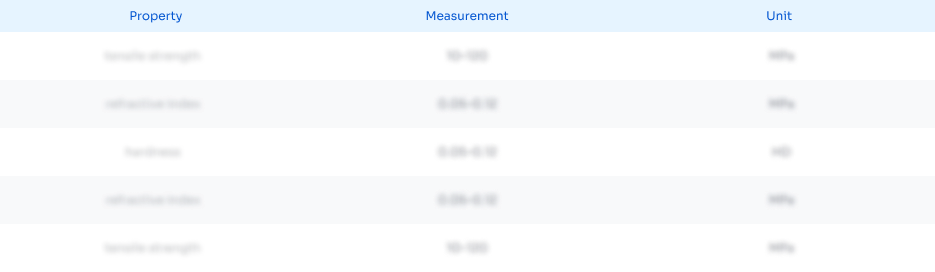
Abstract
Description
Claims
Application Information

- R&D Engineer
- R&D Manager
- IP Professional
- Industry Leading Data Capabilities
- Powerful AI technology
- Patent DNA Extraction
Browse by: Latest US Patents, China's latest patents, Technical Efficacy Thesaurus, Application Domain, Technology Topic, Popular Technical Reports.
© 2024 PatSnap. All rights reserved.Legal|Privacy policy|Modern Slavery Act Transparency Statement|Sitemap|About US| Contact US: help@patsnap.com