Process for producing polycrystalline silicon bar
A manufacturing method, polysilicon technology, applied in the direction of polycrystalline material growth, chemical instruments and methods, silicon, etc., can solve the problems of reduced mechanical strength, reduced life characteristics, increased power costs, etc., to promote the promotion of crystal lattice arrangement, The effect of accelerating the crystal growth rate and improving the life characteristics
- Summary
- Abstract
- Description
- Claims
- Application Information
AI Technical Summary
Problems solved by technology
Method used
Image
Examples
Embodiment 1
[0048] The following examples are given to illustrate the present invention more specifically, but these examples are of course illustrative and should not be limitedly interpreted.
[0049] (Example 1)
[0050] After coating the dry peeling material (high-purity silicon nitride powder) on the inner wall of the silica sintered body sagger (inner size 175mm×350mm), put high-purity silicon raw material into the melting furnace with the same structure as shown in Figure 1, to melt. In Example 1, silicon is melted at 1460°C in a state of slightly pressurized (500 Pa) with hydrogen gas in a melting furnace, and the temperature at the lower part of the sagger is lowered, and the temperature gradient between the upper and lower sides of the sagger is set. The temperature is lowered until the entire sagger reaches 1380°C, the silicon melt is solidified from the lower part of the sagger, and the temperature is further kept at 1380°C for 10 hours to produce polysilicon ingots. The tem...
Embodiment 2
[0054] An ingot was produced in the same manner as in Example 1 under a hydrogen atmosphere using the temperature profile diagram 5 at the same cooling rate of 4° C. / hr as in the melting in an argon atmosphere in Comparative Example 1.
PUM
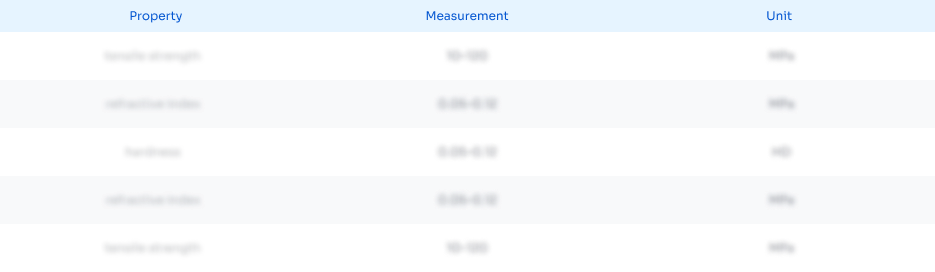
Abstract
Description
Claims
Application Information

- Generate Ideas
- Intellectual Property
- Life Sciences
- Materials
- Tech Scout
- Unparalleled Data Quality
- Higher Quality Content
- 60% Fewer Hallucinations
Browse by: Latest US Patents, China's latest patents, Technical Efficacy Thesaurus, Application Domain, Technology Topic, Popular Technical Reports.
© 2025 PatSnap. All rights reserved.Legal|Privacy policy|Modern Slavery Act Transparency Statement|Sitemap|About US| Contact US: help@patsnap.com