Synthesizing of cyclopentenone
A kind of enone and alkenyl technology, applied in the field of organic synthesis, can solve the problems of low yield, not having high industrial profit, not conducive to the environment, etc.
- Summary
- Abstract
- Description
- Claims
- Application Information
AI Technical Summary
Problems solved by technology
Method used
Image
Examples
Embodiment 1
[0055] Synthesis of 2,3,4,5-tetramethyl-2-cyclopenten-1-one
[0056] a) Preparation of metal catalyst solution
[0057] Contains TiCl 3 (O i The catalytic solution of the Pr) complex can be obtained according to E.V.Vedejs et al. in J.Org.Chem., (1988), 53 , the procedure described in 1593 but applying TiCl 4 and Ti(O i Pr) 4 The complex was obtained as starting material. The amounts used were varied in order to obtain a catalytic solution with a concentration of 1.3 mmoles of metal per gram of catalytic solution.
[0058] All resulting solutions were used without further manipulation.
[0059] b) Preparation of 2,3,4,5-tetramethyl-2-cyclopenten-1-one
[0060] A round bottom flask equipped with a mechanical stirrer, dropping funnel and reflux condenser was charged with 2000 g (23.2 mol) of the starting ketone having 75% w / w acetic acid butyric acid as solvent, 0.35 molar equivalents of anhydrous Magnesium chloride and the aforementioned titanium catalyst solution cont...
Embodiment 2
[0064] Synthesis of 3,4-diethyl-2,5-dimethyl-2-cyclopenten-1-one
[0065] In a round bottom flask equipped with a mechanical stirrer, dropping funnel and reflux condenser, charge 265 g (3.08 mol) of diethyl ketone with 252 g of butyl acetate as solvent, 0.36 molar equivalents of anhydrous magnesium chloride and 0.053 A molar equivalent of the aforementioned titanium catalyst solution of the trichloropropoxytitanium complex. The resulting suspension was vigorously stirred and heated to 85°C. Then 2.1 molar equivalents of propionaldehyde were added dropwise over 2 hours at 85°C. The reaction was continued for an additional hour and cooled to 40°C. The reaction mixture was hydrolyzed with 10% aqueous acetic acid (500 g), decanted and washed with 10% aqueous acetic acid (200 g) and 50 g of sodium chloride. The organic phase was then washed twice with 20% potassium carbonate solution.
[0066] in Na 2 SO 4 After drying, the solvent was evaporated. The crude product (419.6 g)...
Embodiment 3
[0071] Synthesis of various compounds of formula (I)
[0072] General procedure for the cyclopentenone method
[0073] A round bottom flask equipped with a mechanical stirrer, dropping funnel and reflux condenser was charged with 1 molar equivalent of the starting ketone either pure or with 75% w / w butyl acetate as solvent (see below for details) , 0.35 molar equivalent of anhydrous magnesium chloride and the aforementioned titanium catalyst solution containing 0.05 molar equivalent of trichloropropoxytitanium complex. The resulting suspension was vigorously stirred and heated to 90-100°C. Then the aldehyde of formula (III) was added dropwise at 90-100°C over 3 hours. The reaction was continued for an additional hour at 90-100°C and cooled to 40°C. The reaction mixture was hydrolyzed with 10% hydrochloric acid solution, and neutralized with 20% potassium carbonate aqueous solution.
PUM
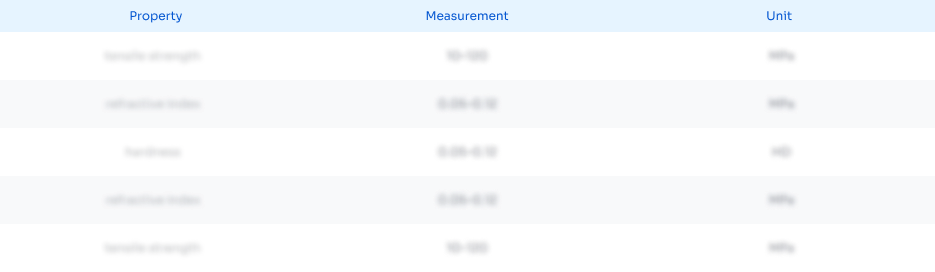
Abstract
Description
Claims
Application Information

- R&D
- Intellectual Property
- Life Sciences
- Materials
- Tech Scout
- Unparalleled Data Quality
- Higher Quality Content
- 60% Fewer Hallucinations
Browse by: Latest US Patents, China's latest patents, Technical Efficacy Thesaurus, Application Domain, Technology Topic, Popular Technical Reports.
© 2025 PatSnap. All rights reserved.Legal|Privacy policy|Modern Slavery Act Transparency Statement|Sitemap|About US| Contact US: help@patsnap.com