Rotary joint structure of underwater electric manipulator
An electric manipulator and rotary joint technology, applied in manipulators, manufacturing tools, joints, etc., can solve the problems of the large volume of the hydraulic manipulator system, the difficulty of achieving a large-depth seal, and the inability to configure the hydraulic system, and it is easy to expand the depth and strength of the operation. , size reduction, wide application effect
- Summary
- Abstract
- Description
- Claims
- Application Information
AI Technical Summary
Problems solved by technology
Method used
Image
Examples
Embodiment Construction
[0017] The present invention will be described in further detail below in conjunction with the accompanying drawings.
[0018] As shown in Figure 1, the present invention includes a stationary end housing 3, a transition piece 5 for a dynamic and static housing, and a driven end housing 8, a central axis 12 passes through the middle of the three in sequence, and one end of the stationary end housing 3 is fixedly connected with a stationary end cover 1. The other end is connected to the transition piece 5 of the dynamic and static housing. One end of the driven end housing 8 is fixedly connected with the driven end cover 11 , and the other end is abutted against the transition piece 5 of the dynamic and static housing. A brake 2 , a torque motor assembly 4 , a harmonic reducer assembly 7 and a rotary encoder 10 are sequentially sleeved on the central shaft 12 from left to right. The brake 2 is accommodated in the space formed by the stationary end cover 1 and the stationary end...
PUM
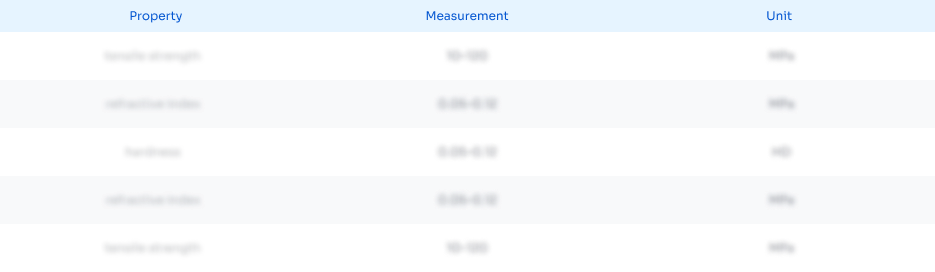
Abstract
Description
Claims
Application Information

- Generate Ideas
- Intellectual Property
- Life Sciences
- Materials
- Tech Scout
- Unparalleled Data Quality
- Higher Quality Content
- 60% Fewer Hallucinations
Browse by: Latest US Patents, China's latest patents, Technical Efficacy Thesaurus, Application Domain, Technology Topic, Popular Technical Reports.
© 2025 PatSnap. All rights reserved.Legal|Privacy policy|Modern Slavery Act Transparency Statement|Sitemap|About US| Contact US: help@patsnap.com