Rolled lubricating process of rolling band-steel
A process method and roll-type technology, applied in the direction of rolls, metal rolling, manufacturing tools, etc., can solve the problems of poor uniformity of lubricating oil, affecting the surface quality of strip steel, and large waste of lubricating oil, so as to avoid surface rolling and sintering, The effect of reducing surface defects of strip steel and reducing lubricating oil consumption
- Summary
- Abstract
- Description
- Claims
- Application Information
AI Technical Summary
Problems solved by technology
Method used
Image
Examples
Embodiment Construction
[0021] see figure 1 , figure 2 , image 3 , a rolling lubrication process for strip steel rolling, is that the rolling lubricating oil 9 is transported to the oiling roller 3 through the oil pipeline 5, and the oiling roller 3 is pressed on the roller with a certain pressure, and is passively moved along with the roller. Rotate, apply rolling oil 9 on the roll surface to form oil film 4, the thickness of oil film 4 is adjusted by the pressure of oiling roll 3 on the roll and the amount of rolling oil supplied. The rolls include an upper work roll 6 , a lower work roll 2 , or an upper back-up roll 7 and a lower back-up roll 1 , and the strip steel 8 is rolled by the upper work roll 6 and the lower work roll 2 .
[0022] see image 3 , the oiling roller 3 is composed of an oiling roller oil seepage layer 15 of the outer layer and an oiling roller shaft 16 of the inner layer, the oiling roller oil seepage layer 15 is made of a composite material that can seep oil, and the oil...
PUM
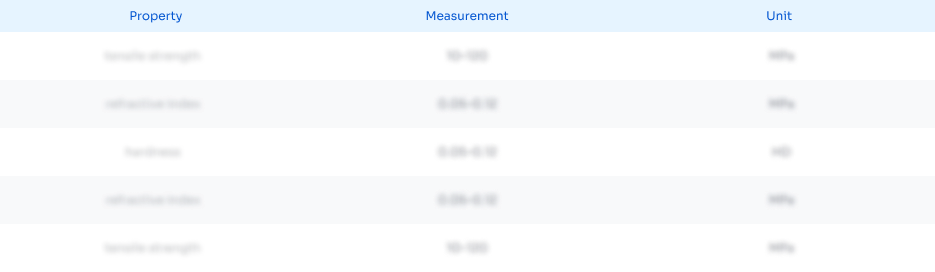
Abstract
Description
Claims
Application Information

- R&D
- Intellectual Property
- Life Sciences
- Materials
- Tech Scout
- Unparalleled Data Quality
- Higher Quality Content
- 60% Fewer Hallucinations
Browse by: Latest US Patents, China's latest patents, Technical Efficacy Thesaurus, Application Domain, Technology Topic, Popular Technical Reports.
© 2025 PatSnap. All rights reserved.Legal|Privacy policy|Modern Slavery Act Transparency Statement|Sitemap|About US| Contact US: help@patsnap.com