Reducing diameter high voltage hollow composite insulator and its manufacturing method
A composite insulator and a manufacturing method of technology, applied in insulators, electrical components, circuits, etc., can solve the problems of poor electrical corrosion and aging resistance of liquid silicone rubber insulation, high center of gravity of straight tubular composite insulators, and easy cracking at bonding places, etc. problems, to achieve uniform laying, reduce the height of the center of gravity and the windward area, and achieve the effect of low cost
- Summary
- Abstract
- Description
- Claims
- Application Information
AI Technical Summary
Problems solved by technology
Method used
Image
Examples
manufacture example 1
[0038] The umbrella body 3 is made of high-temperature vulcanized silicone rubber, and its components are: 25% methyl vinyl silicone rubber, 30% white carbon black, 30% aluminum hydroxide, 4% silicone oil, and 1% vulcanizing agent.
[0039] Manufacturing steps:
[0040] (1), on the mold core 2a of the winding pipe 2 to be wound, fix the pins 2b, 2c according to the two ends of the axis of the simulated trajectory;
[0041] (2) Uninterrupted glass fiber yarn impregnated with epoxy resin is used to wind the mold core to form a hollow tube, and keep the glass fiber evenly wound and the tension constant;
[0042] (3), the hollow tube that step (2) is made carries out high-temperature curing;
[0043] (4), the hollow tube that step (3) is made carries out machining, makes winding tube 2;
[0044] (5), evenly brush the coupling agent on the outer wall;
[0045] (6), place the winding tube 2 in the mold cavity of the injection machine, and close the mold;
[0046] (7) The rubber ...
manufacture example 2
[0051] The umbrella body 3 is made of high-temperature vulcanized silicone rubber, and its components are: 40% methyl vinyl silicone rubber, 50% white carbon black, 35% aluminum hydroxide, 3% silicone oil, and 1% vulcanizing agent.
[0052] Manufacturing steps:
[0053] (1), on the mold core 2a of the winding pipe 2 to be wound, fix the pins 2b, 2c according to the two ends of the axis of the simulated trajectory;
[0054] (2) Uninterrupted glass fiber yarn impregnated with epoxy resin is used to wind the mold core to form a hollow tube, and keep the glass fiber evenly wound and the tension constant;
[0055] (3), the hollow tube that step (2) is made carries out high-temperature curing;
[0056] (4), the hollow tube that step (3) is made carries out machining, makes winding tube 2;
[0057] (5), evenly brush the coupling agent on the outer wall;
[0058] (6), place the winding tube 2 in the mold cavity of the injection machine, and close the mold;
[0059] (7) The rubber ...
PUM
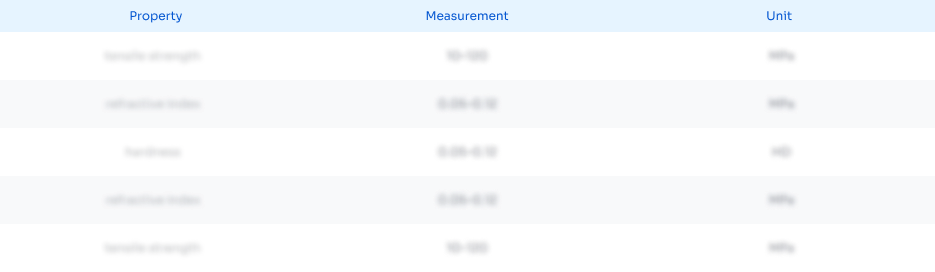
Abstract
Description
Claims
Application Information

- R&D
- Intellectual Property
- Life Sciences
- Materials
- Tech Scout
- Unparalleled Data Quality
- Higher Quality Content
- 60% Fewer Hallucinations
Browse by: Latest US Patents, China's latest patents, Technical Efficacy Thesaurus, Application Domain, Technology Topic, Popular Technical Reports.
© 2025 PatSnap. All rights reserved.Legal|Privacy policy|Modern Slavery Act Transparency Statement|Sitemap|About US| Contact US: help@patsnap.com