Apparatus for fabricating optical fiber preform and method for fabricating low water peak fiber using the same
An optical fiber preform and preform technology, which can be applied to manufacturing tools, glass manufacturing equipment, etc., can solve the problems of manufacturing cost and time of elongating the first optical fiber preform.
- Summary
- Abstract
- Description
- Claims
- Application Information
AI Technical Summary
Problems solved by technology
Method used
Image
Examples
Embodiment Construction
[0030] Embodiments of the present invention are described below with reference to the drawings. For clarity and simplicity, detailed descriptions of well-known functions and constructions incorporated herein are omitted to avoid obscuring the subject matter of the present invention.
[0031] FIG. 2 is a flowchart illustrating an optical fiber preform manufacturing method according to a preferred embodiment of the present invention, and FIGS. 3 to 12 are views illustrating its steps for manufacturing an optical fiber preform. The method for manufacturing an optical fiber preform includes steps (a), (b), (c), (d), (e) and (f): S21 , S22 , S23 , S24 , S25 and S26 in FIG. 2 .
[0032] Step (a) S21 is a process of growing a first soot preform on the starting member along the longitudinal direction of the starting member by soot deposition.
[0033] FIG. 3 is a view illustrating step (a) S21 of growing the first soot preform. The apparatus 100 for manufacturing an optical fiber pr...
PUM
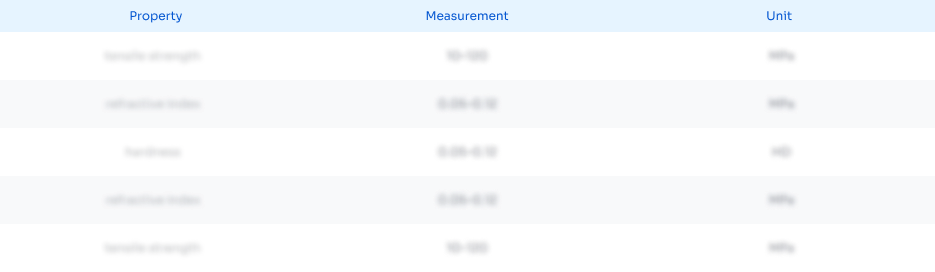
Abstract
Description
Claims
Application Information

- R&D
- Intellectual Property
- Life Sciences
- Materials
- Tech Scout
- Unparalleled Data Quality
- Higher Quality Content
- 60% Fewer Hallucinations
Browse by: Latest US Patents, China's latest patents, Technical Efficacy Thesaurus, Application Domain, Technology Topic, Popular Technical Reports.
© 2025 PatSnap. All rights reserved.Legal|Privacy policy|Modern Slavery Act Transparency Statement|Sitemap|About US| Contact US: help@patsnap.com