Method and device for washing wet-process zinc metallurgy output slag
A technology of wet zinc smelting and washing method, applied in the field of smelting methods and devices, can solve the problems of difficult volume balance, system volume expansion, large water consumption, etc., and achieves the effects of good washing, overcoming short circuit, and less water consumption
- Summary
- Abstract
- Description
- Claims
- Application Information
AI Technical Summary
Problems solved by technology
Method used
Image
Examples
Embodiment 1
[0033] A factory has a device with an annual output of 5,000 tons of zinc. The raw material is secondary zinc oxide containing about 45% zinc. The conventional two-stage leaching method is adopted, and the leaching slag filter press equipment is 80m 2 Chamber filter press 3, each machine can filter 2.5-2.8 tons of dry residue. Use the method and device of the present invention to wash the slag produced by hydrometallurgy, and the device includes a box filter press 3, an intermediate tank 4, and an ore slurry that connects the box filter press 3 and the intermediate tank 4 into a circulation system Pump 5 and pipes, two water storage barrels for filling water into the middle tank 4, one is a clear water barrel 2 for storing clean water, and the other is an anti-pickling bucket 1 for storing washing water, and the volume of the water storage barrel is the chamber filter press 3 Twice the volume of the filter chamber, that is, 2.5 to 3 cubic meters.
[0034] It washes after the ...
Embodiment 2
[0048] A certain factory has an annual output of 8,000 tons of zinc per year, using the conventional iron vitriol method, and the vitriol slag filter press equipment is 80m 2 Chamber filter press 3, with a daily output of 20t-25t of alum slag, and the amount of dry residue filtered by each machine is about 2.3t-2.5t each time. Use the method and device of the present invention to wash the jarosite slag, and its device includes a chamber filter press 3, an intermediate tank 4, and a slurry pump 5 and pipelines that connect the chamber filter press 3 and the intermediate tank 4 into a circulation system , two water storage buckets for filling water into the middle tank 4, one is a clean water bucket 2 for storing clean water, and the other is an anti-pickling bucket 1 for storing washing water, and the volume of the water storage bucket is the volume of the chamber filter press 3 Twice as much, that is, 2.5 to 3 cubic meters.
[0049] It washes after the filter press is complet...
PUM
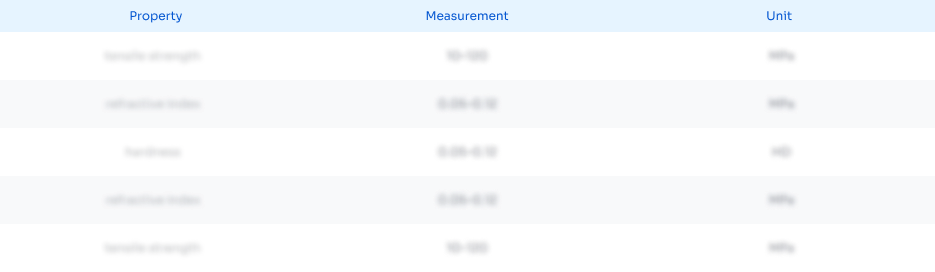
Abstract
Description
Claims
Application Information

- Generate Ideas
- Intellectual Property
- Life Sciences
- Materials
- Tech Scout
- Unparalleled Data Quality
- Higher Quality Content
- 60% Fewer Hallucinations
Browse by: Latest US Patents, China's latest patents, Technical Efficacy Thesaurus, Application Domain, Technology Topic, Popular Technical Reports.
© 2025 PatSnap. All rights reserved.Legal|Privacy policy|Modern Slavery Act Transparency Statement|Sitemap|About US| Contact US: help@patsnap.com