Modified chlorosulphonated polyethylene rubber paint for steel storage tank and preparation method thereof
A chlorosulfonated polyethylene and rubber coating technology, applied in epoxy resin coatings, coatings, containers, etc., can solve the problem of poor salt spray resistance and light aging resistance, and the coating is prone to pitting corrosion, discoloration and chalking. and other problems, to achieve the effect of improving thixotropy and workability, improving storage stability, and improving solvent resistance
- Summary
- Abstract
- Description
- Claims
- Application Information
AI Technical Summary
Problems solved by technology
Method used
Examples
Embodiment 1
[0017] The manufacturing process of the modified chlorosulfonated polyethylene rubber coating for steel storage tanks in the present embodiment 1 is: in a stainless steel bucket, 1 part by weight of chlorosulfonated polyethylene rubber is added to 1 part by weight of chlorosulfonated polyethylene rubber Add polyethylene rubber into 3.0 parts by weight of xylene and 1 part by weight of trimethylbenzene mixed solvent, stir evenly at low speed at room temperature, and disperse at high speed for 5 hours, add 0.1 part by weight of titanium dioxide, 0.2 part by weight of titanium dioxide while stirring Part of talcum powder, 0.02 parts by weight of AFCONA-3777 fluorocarbon modified polyacrylate, 0.02 parts by weight of organic bentonite 881, after dispersing for 0.5h, grind for 1h with a sand mill to make the A agent of the coating; Add 3.5 parts by weight of xylene and 0.8 parts by weight of n-butanol in the bisphenol A type epoxy resin of 1 part, mix well, under the situation of hi...
Embodiment 2
[0022] The manufacturing process of the modified chlorosulfonated polyethylene rubber coating for steel storage tanks in the present embodiment 2 is: in a stainless steel bucket, 1 part by weight of chlorosulfonated polyethylene rubber is added to 1 part by weight of chlorosulfonated polyethylene rubber Add polyethylene rubber into 2.5 parts by weight of xylene and 1.5 parts by weight of trimethylbenzene mixed solvent, stir evenly at low speed at room temperature, and disperse at high speed for 5 hours, add 0.2 parts by weight of titanium dioxide, 0.3 parts by weight of titanium dioxide while stirring Parts of talcum powder, 0.01 parts by weight of EFKA-3777 fluorocarbon modified polyacrylate, 0.03 parts by weight of organic bentonite 881, after dispersing for 0.5h, grind for 1h with a sand mill to make the A agent of the coating; Add 3.5 parts by weight of xylene and 0.8 parts by weight of n-butanol in the bisphenol A type epoxy resin of 1 part, mix well, under the situation o...
Embodiment 3
[0025]The manufacturing process of the modified chlorosulfonated polyethylene rubber coating for steel storage tanks in this embodiment 3 is: in a stainless steel bucket, 1 part by weight of chlorosulfonated polyethylene rubber is added to Add polyethylene rubber into 2.0 parts by weight of xylene and 2.1 parts by weight of trimethylbenzene mixed solvent, stir evenly at low speed at room temperature, and disperse at high speed for 5 hours, then add 0.18 parts by weight of titanium dioxide while stirring , 0.25 parts by weight of talcum powder, 0.03 parts by weight of AFCONA-3777 fluorocarbon modified polyacrylate, 0.05 parts by weight of organic bentonite, after dispersing for 0.5h, grind 1h with a sand mill to make the A agent of the coating; Add 3.5 parts by weight of xylene and 0.8 parts by weight of n-butanol to 1 part by weight of bisphenol A epoxy resin, mix well, and add 0.1 parts by weight of diphenylguanidine, 0.1 parts by weight of ethylene thiourea, dispersed for 0....
PUM
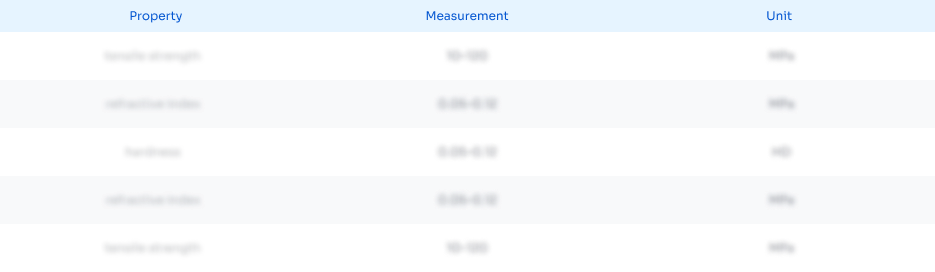
Abstract
Description
Claims
Application Information

- Generate Ideas
- Intellectual Property
- Life Sciences
- Materials
- Tech Scout
- Unparalleled Data Quality
- Higher Quality Content
- 60% Fewer Hallucinations
Browse by: Latest US Patents, China's latest patents, Technical Efficacy Thesaurus, Application Domain, Technology Topic, Popular Technical Reports.
© 2025 PatSnap. All rights reserved.Legal|Privacy policy|Modern Slavery Act Transparency Statement|Sitemap|About US| Contact US: help@patsnap.com