Method of preparing biological diesel oil from high acid value abandoned grease by titanium tetrachloride catalysts
A technology of titanium tetrachloride catalyzing high acid and waste oil, applied in the field of oleochemistry, can solve the problems of high raw material requirements, harsh conditions, high price, etc., and achieve the effects of simple production process, mild reaction conditions and high industrial value
- Summary
- Abstract
- Description
- Claims
- Application Information
AI Technical Summary
Problems solved by technology
Method used
Image
Examples
Embodiment 1
[0031] Add 100 grams of pretreated waste hot pot oil and 42 grams of methanol (oleyl alcohol molar ratio 1:12) into the reactor, and add 2 grams of titanium tetrachloride (2% of the fat weight) at the same time. Heated and maintained at 65°C to 70°C, stirred and refluxed for 6h. The reactants were separated into two layers after standing for 0.5h, the upper layer was higher fatty acid methyl ester liquid containing a small amount of methanol and titanium tetrachloride, and the lower layer was glycerin, titanium tetrachloride and excess methanol. The upper liquid is distilled at 65°C-70°C to remove residual methanol and recycled. The residue is higher fatty acid methyl ester containing titanium tetrachloride, washed with a small amount of water until neutral, filtered to remove impurities, and dried. Biodiesel products are available. The yield was 90.5%.
Embodiment 2
[0033] Add 100 grams of pretreated waste hot pot oil and 42 grams of methanol (oleyl-alcohol molar ratio 1:12) into the reactor, and add 5 grams of titanium tetrachloride (5% of the fat weight) at the same time. Heated and maintained at 65°C to 70°C, stirred and refluxed for 5h. The reactants were separated into two layers after standing for 0.5h, the upper layer was higher fatty acid methyl ester liquid containing a small amount of methanol and titanium tetrachloride, and the lower layer was glycerin, titanium tetrachloride and excess methanol. The upper liquid is distilled at 65°C-70°C to remove residual methanol and recycled. The residue is higher fatty acid methyl ester containing titanium tetrachloride, washed with a small amount of water until neutral, filtered to remove impurities, and dried. Biodiesel products are available. The yield was 92.3%.
Embodiment 3
[0035] Add 100 grams of pretreated waste hot pot oil and 42 grams of methanol (oleyl-alcohol molar ratio 1:12) into the reactor, and add 10 grams of titanium tetrachloride (10% of the fat weight) at the same time. Heated and maintained at 65°C to 70°C, stirred and refluxed for 4h. The reactants were separated into two layers after standing for 0.5h, the upper layer was higher fatty acid methyl ester liquid containing a small amount of methanol and titanium tetrachloride, and the lower layer was glycerin, titanium tetrachloride and excess methanol. The upper liquid is distilled at 65°C-70°C to remove residual methanol and recycled. The residue is higher fatty acid methyl ester containing titanium tetrachloride, washed with a small amount of water until neutral, filtered to remove impurities, and dried. Biodiesel products are available. The yield is 94.5%.
PUM
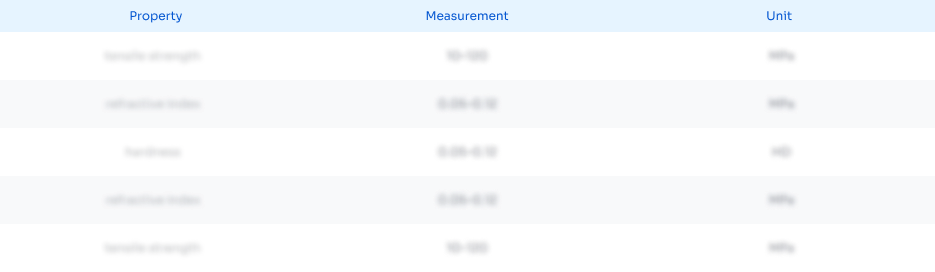
Abstract
Description
Claims
Application Information

- R&D
- Intellectual Property
- Life Sciences
- Materials
- Tech Scout
- Unparalleled Data Quality
- Higher Quality Content
- 60% Fewer Hallucinations
Browse by: Latest US Patents, China's latest patents, Technical Efficacy Thesaurus, Application Domain, Technology Topic, Popular Technical Reports.
© 2025 PatSnap. All rights reserved.Legal|Privacy policy|Modern Slavery Act Transparency Statement|Sitemap|About US| Contact US: help@patsnap.com