Ion implantation process to raise anticorrosion performance of lumpy amorphous alloy
A technology of ion implantation and amorphous alloy, which is applied in the direction of ion implantation plating, metal material coating process, coating, etc., can solve the problems of poor corrosion performance and limit commercial applications, and improve corrosion resistance, energy and dose Precise and Controllable Effects
- Summary
- Abstract
- Description
- Claims
- Application Information
AI Technical Summary
Problems solved by technology
Method used
Image
Examples
Embodiment 1
[0014] Step 1: La with a purity of 99.6%, Al with a purity of 99.5%, Cu with a purity of 99.95%, Ag with a purity of 99.8%, Ni with a purity of 99.8%, and Co with a purity of 99.9% were prepared by La 62 Al 14 (Cu 5 / 6 Ag 1 / 6 ) 14 Ni 5 co 5 The ratio is arc smelted in an argon atmosphere adsorbed by zirconium to obtain a uniformly mixed alloy ingot.
[0015] Step 2: Melt the ingot obtained in Step 1 on a water-cooled copper mold in an argon-protected melting furnace.
[0016] Step 3: inject the alloy solution obtained in step 2 into a water-cooled copper mold with an inner diameter of 5 mm by using the pressure difference. A bulk amorphous alloy is produced.
[0017] Step 4: Use MEVVA source ion implanter to implant Nb ions into La 62 Al 14 (Cu 5 / 6 Ag 1 / 6 ) 14 Ni 5 co 5 Bulk metallic glass surface, injection dose: 1×10 16 -1×10 17 Nb / cm 2 .
[0018] Step 5: Characterize the structure of the bulk amorphous before and after ion implantation by X-ray diffraction ...
Embodiment 2
[0022] Step 1: La with a purity of 99.6%, Al with a purity of 99.5%, Cu with a purity of 99.95%, Ag with a purity of 99.8%, Ni with a purity of 99.8%, and Co with a purity of 99.9% were prepared by La 62 Al 14 (Cu 5 / 6 Ag 1 / 6 ) 14 Ni 5 co 5 The ratio is arc smelted in an argon atmosphere adsorbed by zirconium to obtain a uniformly mixed alloy ingot.
[0023] Step 2: Melt the ingot obtained in Step 1 on a water-cooled copper mold in an argon-protected melting furnace.
[0024] Step 3: inject the alloy solution obtained in step 2 into a water-cooled copper mold with an inner diameter of 5 mm by using the pressure difference. A bulk amorphous alloy is produced.
[0025] Step 4: Use MEVVA source ion implanter to implant Ta ions into La 62 Al 14 (Cu 5 / 6 Ag 1 / 6 ) 14 Ni 5 co 5 Bulk metallic glass surface, injection dose: 1×10 16 -1×10 17 Ta / cm 2 .
[0026] Step 5: Characterize the structure of the bulk amorphous before and after ion implantation by X-ray diffraction....
Embodiment 3
[0029] Step 1: La with a purity of 99.6%, Al with a purity of 99.5%, Cu with a purity of 99.95%, Ag with a purity of 99.8%, Ni with a purity of 99.8%, and Co with a purity of 99.9% were prepared by La 62 Al 14 (Cu 5 / 6 Ag 1 / 6 ) 14 Ni 5 co 5 The ratio is arc smelted in an argon atmosphere adsorbed by zirconium to obtain a uniformly mixed alloy ingot.
[0030] Step 2: Melt the ingot obtained in Step 1 on a water-cooled copper mold in an argon-protected melting furnace.
[0031] Step 3: inject the alloy solution obtained in step 2 into a water-cooled copper mold with an inner diameter of 5 mm by using the pressure difference. A bulk amorphous alloy is produced.
[0032] Step 4: Use MEVVA source ion implanter to implant Cr ions into La 62 Al 14 (Cu 5 / 6 Ag 1 / 6 ) 14 Ni 5 co 5 Bulk metallic glass surface, injection dose: 1×10 16 -1×10 17 Cr / cm 2 .
[0033] Step 5: Characterize the structure of the bulk amorphous before and after ion implantation by X-ray diffraction....
PUM
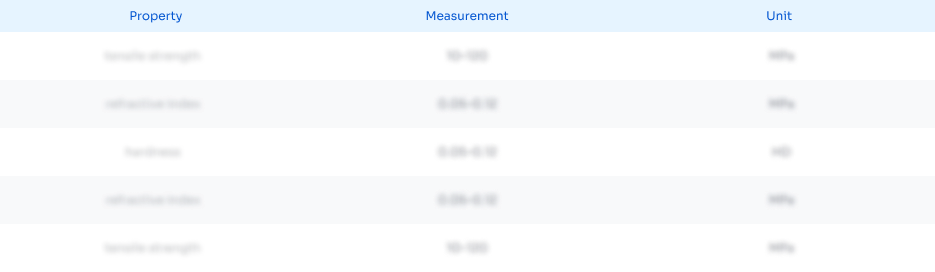
Abstract
Description
Claims
Application Information

- R&D
- Intellectual Property
- Life Sciences
- Materials
- Tech Scout
- Unparalleled Data Quality
- Higher Quality Content
- 60% Fewer Hallucinations
Browse by: Latest US Patents, China's latest patents, Technical Efficacy Thesaurus, Application Domain, Technology Topic, Popular Technical Reports.
© 2025 PatSnap. All rights reserved.Legal|Privacy policy|Modern Slavery Act Transparency Statement|Sitemap|About US| Contact US: help@patsnap.com