Capacitor MEMS acceleration sensor
An acceleration sensor, capacitive technology, applied in the direction of measuring acceleration, speed/acceleration/shock measurement, instruments, etc., can solve the problem of increasing the cost of the sensor, achieve simple structure, reduce production conditions and costs, and reduce damping effects
- Summary
- Abstract
- Description
- Claims
- Application Information
AI Technical Summary
Problems solved by technology
Method used
Image
Examples
Embodiment Construction
[0018] from figure 1 It can be seen that a capacitive MEMS acceleration sensor includes an upper electrode 1, a lower electrode 3 and a movable middle electrode. The middle electrode moves up and down under the action of acceleration, and together with the upper and lower electrodes forms a variable-pitch differential capacitor. The upper electrode 1 and the lower electrode 3 can be made of high silica glass or single crystal silicon. They are grooved electrodes formed by micromachining techniques. The upper electrode 1 and the lower electrode 3 also play the role of overload protection. The middle electrode is sandwiched between the upper electrode 1 and the lower electrode 3, which is based on single crystal silicon with [100] crystal orientation, and is formed by micromachining technology to form an integrated body including frame 4, mass block 2, cantilever beam 5, etc. Composite beam structure. The proof mass 2 is supported by a cantilever beam 5 and the like, and is ...
PUM
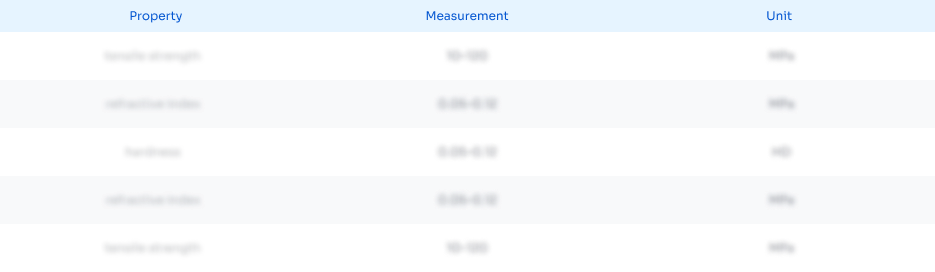
Abstract
Description
Claims
Application Information

- R&D
- Intellectual Property
- Life Sciences
- Materials
- Tech Scout
- Unparalleled Data Quality
- Higher Quality Content
- 60% Fewer Hallucinations
Browse by: Latest US Patents, China's latest patents, Technical Efficacy Thesaurus, Application Domain, Technology Topic, Popular Technical Reports.
© 2025 PatSnap. All rights reserved.Legal|Privacy policy|Modern Slavery Act Transparency Statement|Sitemap|About US| Contact US: help@patsnap.com