Oil remover and its production
A technology of deoiling agent and oxidizing agent, which is applied in the direction of separation methods, chemical instruments and methods, and other chemical processes, can solve the problems of reduced conversion catalyst activity, reduced catalyst catalytic activity, and reduced production efficiency, etc., to achieve low production costs, Maintain the use effect and use time, and the effect of high degreasing efficiency
- Summary
- Abstract
- Description
- Claims
- Application Information
AI Technical Summary
Problems solved by technology
Method used
Examples
Embodiment 1
[0021] Take 15% bentonite, 82% lignite, and 3% sodium chloride by weight, grind them to 100 mesh, add water to moisten them, mix them evenly with a mixer, and extrude them into Φ3.5-4.5mm and 4mm lengths with an extruder After being dried in a drying furnace, it is sent into a roasting furnace for 25 hours of roasting at a roasting temperature of 700°C, cooled, screened, and packaged.
Embodiment 2
[0023] The steps of preparing degreasing agent are as follows:
[0024] Take diatomite with a weight ratio of 20%, 75% furfural slag, and 5% sodium chloride, pulverize to 100 mesh, add water to moisten, mix with a mixer, and use a forming machine to form a Φ4mm spherical shape, and dry it in a furnace After drying, it is sent into a roasting furnace for roasting for 50 hours at a roasting temperature of 700°C, cooled, screened, and packaged.
Embodiment 3
[0026] The steps of preparing degreasing agent are as follows:
[0027] Get the zeolite that is 15% by weight, the lignite of 81%, the potassium chloride of 4%, pulverize to 100
[0028] Take 15% zeolite, 81% lignite, and 4% potassium chloride by weight, grind them to 100 mesh, add water to moisten them, mix them evenly with a mixer, and extrude them into Φ3.5-4.5mm long 10mm cylindrical shape, after drying in a drying furnace, send it to a roasting furnace for 10 hours of roasting at a roasting temperature of 800°C, cooling, screening, and packaging.
PUM
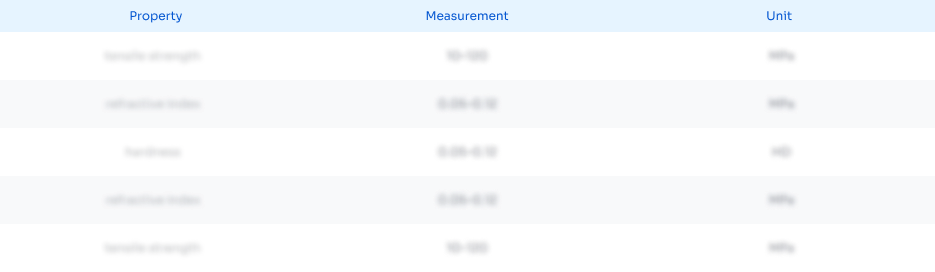
Abstract
Description
Claims
Application Information

- Generate Ideas
- Intellectual Property
- Life Sciences
- Materials
- Tech Scout
- Unparalleled Data Quality
- Higher Quality Content
- 60% Fewer Hallucinations
Browse by: Latest US Patents, China's latest patents, Technical Efficacy Thesaurus, Application Domain, Technology Topic, Popular Technical Reports.
© 2025 PatSnap. All rights reserved.Legal|Privacy policy|Modern Slavery Act Transparency Statement|Sitemap|About US| Contact US: help@patsnap.com