High-temperature-resistant high-pressure-resistant ceramic strain gauge sensor and its package curing method
A technology of strain gauge and high pressure resistance, which is applied in the packaging and curing field of sensors and ceramic strain gauge sensors, can solve the problems of limited service life of molded products, small signal receiving range, poor temperature and pressure resistance, etc., and achieve small deformation, Effects of improving reception width and repeatability, and improving wear resistance
- Summary
- Abstract
- Description
- Claims
- Application Information
AI Technical Summary
Problems solved by technology
Method used
Image
Examples
Embodiment 1
[0034] The encapsulation and curing method of the sensor is carried out in the following steps:
[0035] 1) Clean the ceramic strain gauge, sensor housing and strain gauge holder with solvent oil;
[0036] 2) Put the ceramic strain gauge into the strain gauge fixing seat, and weld the electrode lead wires, and pay attention to face the negative electrode upward;
[0037] 3), weighing 1.5-2.5 grams of high-temperature epoxy resin A and curing agent B according to the ratio of 1:1, and placing them in two containers respectively, the carbonization temperature of the high-temperature epoxy resin is below 300°C;
[0038] 4) Put the weighed high-temperature epoxy resin and the installed sensor components together into the incubator, and preheat for 1.5 hours at a constant temperature of 75°C to 85°C;
[0039] 5) Take out the preheated high-temperature epoxy resin, and quickly pour high-temperature epoxy resin A and curing agent B into a container and stir evenly, try to keep the h...
Embodiment 2
[0045] The encapsulation and curing method of the sensor is carried out in the following steps:
[0046] 1) Clean the ceramic strain gauge, sensor housing and strain gauge holder with solvent oil;
[0047] 2) Put the ceramic strain gauge into the strain gauge fixing seat, and weld the electrode lead wires, and pay attention to face the negative electrode upward;
[0048] 3), weighing 1.8-2.3 grams of high-temperature epoxy resin A and curing agent B according to the ratio of 1:1, and placing them in two containers respectively, the carbonization temperature of the high-temperature epoxy resin is below 300°C;
[0049] 4) Put the weighed high-temperature epoxy resin and the installed sensor components together into the incubator, and preheat for 1.5 hours at a constant temperature of 77°C to 83°C;
[0050] 5) Take out the preheated high-temperature epoxy resin, and quickly pour high-temperature epoxy resin A and curing agent B into a container and stir evenly, try to keep the h...
PUM
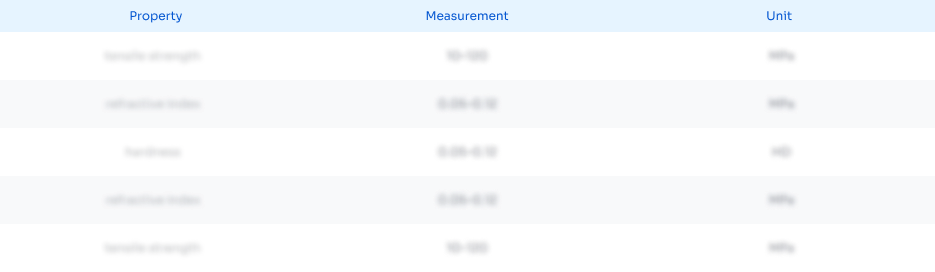
Abstract
Description
Claims
Application Information

- Generate Ideas
- Intellectual Property
- Life Sciences
- Materials
- Tech Scout
- Unparalleled Data Quality
- Higher Quality Content
- 60% Fewer Hallucinations
Browse by: Latest US Patents, China's latest patents, Technical Efficacy Thesaurus, Application Domain, Technology Topic, Popular Technical Reports.
© 2025 PatSnap. All rights reserved.Legal|Privacy policy|Modern Slavery Act Transparency Statement|Sitemap|About US| Contact US: help@patsnap.com