Cemented oil tank and its producing method
A manufacturing method and technology for fuel tanks, which are applied to the substructure and other directions, can solve the problems of high investment cost of laser welding equipment, unsatisfactory welding quality of fuel tanks, and poor welding effect of dissimilar materials, so as to improve operation safety and reduce dependence. performance and reduce maintenance costs
- Summary
- Abstract
- Description
- Claims
- Application Information
AI Technical Summary
Problems solved by technology
Method used
Image
Examples
Embodiment Construction
[0039] Such as image 3 As shown, the manufacturing method of the glued fuel tank of the present invention includes the following steps:
[0040] Material preparation step 21
[0041] Such as Figure 4 As shown, in the material preparation step 21, materials are selected, such as SPCEN steel plates, to form upper and lower box units 31, 32 and connecting pipes 33.
[0042] The upper case unit 31 has an upper case 311, an oil inlet 312 formed on the upper case 311, an outer flange 313 protruding from the upper case 311 around the periphery of the oil inlet 312, and a hollow annular oil pump fixing seat 314 .
[0043] Such as Figure 4 , Figure 6 As shown, the upper box body 311 includes a stepped mounting surface 315, an upright portion 310 and a flat portion 310' forming an outer periphery.
[0044] The stepped mounting surface 315 defines a mounting opening 317 that gradually widens outward.
[0045] The upright portion 310 and the plane portion 310' are connected to each other ...
PUM
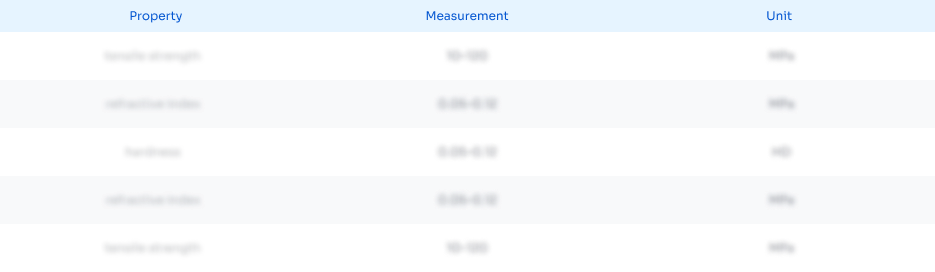
Abstract
Description
Claims
Application Information

- R&D
- Intellectual Property
- Life Sciences
- Materials
- Tech Scout
- Unparalleled Data Quality
- Higher Quality Content
- 60% Fewer Hallucinations
Browse by: Latest US Patents, China's latest patents, Technical Efficacy Thesaurus, Application Domain, Technology Topic, Popular Technical Reports.
© 2025 PatSnap. All rights reserved.Legal|Privacy policy|Modern Slavery Act Transparency Statement|Sitemap|About US| Contact US: help@patsnap.com