Composite heat insulation concrete wall and its construction method
A heat-insulating concrete and composite thermal insulation technology, which is applied in the direction of thermal insulation, walls, and structural elements, can solve the problems of lack of fixed points for composite thermal insulation concrete walls, difficulty in wall decoration, and delay in construction time. Body decoration, flexible design, anti-cracking effect
- Summary
- Abstract
- Description
- Claims
- Application Information
AI Technical Summary
Problems solved by technology
Method used
Image
Examples
Embodiment Construction
[0040] Referring to Figures 1, 2, 3 and 4 for the embodiments, the thermal insulation layer of this composite concrete wall doubles as a wall template, and the concrete wall base 2 is poured in the wall template 1.
[0041] See Figures 1, 2, and 3. The wall formwork is composed of two polystyrene foam side formworks arranged in parallel. There are steel sheets built into the boards, and the connecting steel bars are connected between the two boards. The two rows of built-in steel sheets 11 are opposite and uniform. Distributed at intervals and vertically embedded in the polystyrene foam board side formwork, its cross section is Π-shaped, with concave-convex teeth 13 on the edges of the two bending surfaces, and through holes 14 are opened on the concave-convex teeth. The concave-convex teeth and The through hole is exposed on the inner surface of the side formwork of the polystyrene foam plastic board. The connecting steel bar 12 is in the shape of ], and the hooks at both ends...
PUM
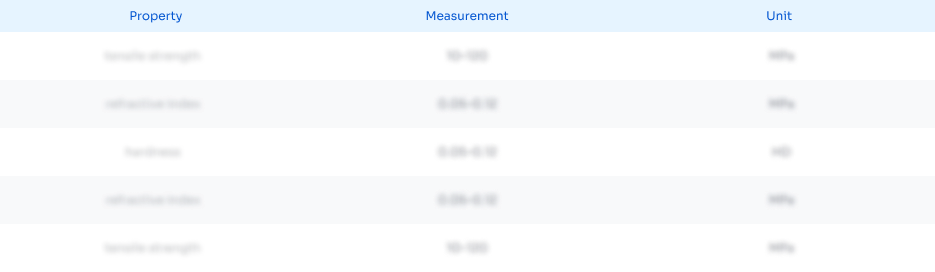
Abstract
Description
Claims
Application Information

- R&D
- Intellectual Property
- Life Sciences
- Materials
- Tech Scout
- Unparalleled Data Quality
- Higher Quality Content
- 60% Fewer Hallucinations
Browse by: Latest US Patents, China's latest patents, Technical Efficacy Thesaurus, Application Domain, Technology Topic, Popular Technical Reports.
© 2025 PatSnap. All rights reserved.Legal|Privacy policy|Modern Slavery Act Transparency Statement|Sitemap|About US| Contact US: help@patsnap.com