Technology and apparatus for forming worm channel with plastic liner of centrifugal pump
一种成型方法、离心泵的技术,应用在泵、泵元件、非变容式泵等方向,能够解决生产效率低、离心泵效率和水力特性下降、防腐耐磨性能下降等问题,达到提高衬塑效率和成品率、提高效率及水力特性、节约生产成本的效果
- Summary
- Abstract
- Description
- Claims
- Application Information
AI Technical Summary
Problems solved by technology
Method used
Image
Examples
Embodiment
[0014] Embodiment: Referring to the accompanying drawings, the metal volute 1 of an involute centrifugal pump is used as the outer mold, and a circular or approximately circular flow path with a certain thickness is obtained as a lining by a molding method. Ultra-high molecular weight polyethylene or polypropylene lining plastic layer 2 (Figure 1). Then, the milling template 4 ( FIG. 2 ) with the volute flow channel 3 matched with the front pump cover is fixed on the front pump cover side of the metal pump body 1 ( FIG. 7 ) through the fixing screw hole 5 . In order to facilitate accurate positioning, the inside of the milling template is provided with a positioning convex ring 6 (Fig. 3). Bearing 7 (Fig. 4) is provided in the positioning sleeve at the location of the milling mold runner track corresponding to the tool handle 8 of the milling cutter 9 having the same width as the runner. During the cutting process, the bearing on the milling tool shank is attached to the inne...
PUM
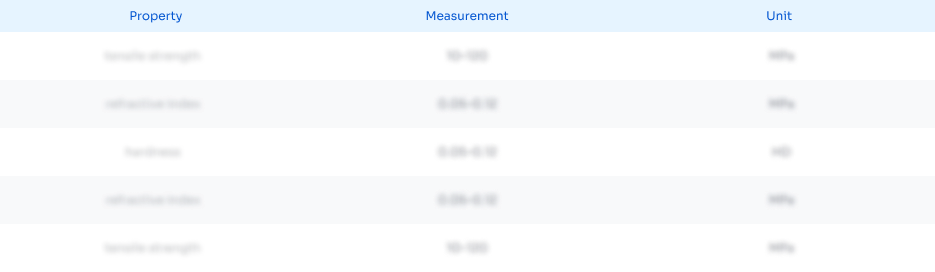
Abstract
Description
Claims
Application Information

- R&D
- Intellectual Property
- Life Sciences
- Materials
- Tech Scout
- Unparalleled Data Quality
- Higher Quality Content
- 60% Fewer Hallucinations
Browse by: Latest US Patents, China's latest patents, Technical Efficacy Thesaurus, Application Domain, Technology Topic, Popular Technical Reports.
© 2025 PatSnap. All rights reserved.Legal|Privacy policy|Modern Slavery Act Transparency Statement|Sitemap|About US| Contact US: help@patsnap.com