Lifting mechanism braking system of hoister
A lifting mechanism and braking system technology, applied in the direction of spring mechanism, load hanging components, hoisting device, etc., can solve problems such as equipment damage, accelerated descent, equipment and staff injury, etc., to ensure safety, Effect of reducing impact load and avoiding damage to parts
- Summary
- Abstract
- Description
- Claims
- Application Information
AI Technical Summary
Problems solved by technology
Method used
Image
Examples
Embodiment Construction
[0018] As shown in Figure 1, it is the braking system of the hoisting mechanism of the single drum of the crane; the mechanical transmission chain of the hoisting mechanism of the crane is composed of the motor 1, the coupling 2, the reducer 6 and the drum 5. As shown in Figure 2, the braking system of the double-drum hoisting mechanism consists of a motor 1, a coupling 2, a central reducer 7, a coupling 8 with a floating shaft, a secondary reducer 9 and a drum 5. The mechanical transmission chain of the lifting mechanism. The braking system of the hoisting mechanism includes: the mechanical transmission chain of the hoisting mechanism; a pulse encoder is installed at the shaft end of the motor on the mechanical transmission chain, a pulse encoder is installed at the shaft end of the reel, and an overspeed switch for detecting the motor speed, etc. A fault detection element 11; a working brake 3 is installed on the high-speed shaft of the reducer in the mechanical transmission...
PUM
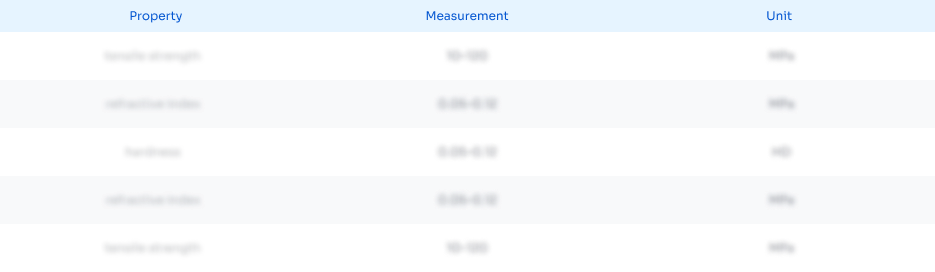
Abstract
Description
Claims
Application Information

- R&D
- Intellectual Property
- Life Sciences
- Materials
- Tech Scout
- Unparalleled Data Quality
- Higher Quality Content
- 60% Fewer Hallucinations
Browse by: Latest US Patents, China's latest patents, Technical Efficacy Thesaurus, Application Domain, Technology Topic, Popular Technical Reports.
© 2025 PatSnap. All rights reserved.Legal|Privacy policy|Modern Slavery Act Transparency Statement|Sitemap|About US| Contact US: help@patsnap.com