Chinlon 6 filament iso-shrinkage air multi-textured yarn processing method
A processing method and technology of shrinking air, applied in textiles and papermaking, etc., can solve problems such as poor layering, rigidity, and single shape and structure of deformed yarns, and achieve good bulkiness, strong hairy feeling, and fine yarn body structure Effect
- Summary
- Abstract
- Description
- Claims
- Application Information
AI Technical Summary
Problems solved by technology
Method used
Image
Examples
Embodiment 1
[0034] Nylon 6 pre-drawn yarn is selected as the raw material. The core layer A component of the raw material is an ordinary circular cross-section filament, and the B component and C component are both trilobal cross-section filaments, a total of 3 components; After the shrinkage yarn preparation process, the improved process on the parallel drawing machine is as follows: the number of fibers in component A is 36, the drafting ratio is 1.3 times, the temperature of the hot plate is 130°C, the number of fibers in component B is 36, and the drafting ratio is 1.3 times. The multiple is 1.5 times, the hot plate temperature is 140°C, the number of C component fibers is 20, the draft ratio is 1.9 times, and the hot plate temperature is 150°C to prepare 3-component nylon 6 filament different shrinkage composite yarn; then Its input air deformation process, the improved process on its air deformation machine: (1) the overfeed rate is 175% (2) the air pressure of the air nozzle is 8Kg / ...
Embodiment 2
[0036] Nylon 6 pre-drawn yarn is selected as the raw material. The core layer A component of the raw material is an ordinary circular cross-section filament; Components and G components use pentagonal cross-section filaments, a total of 7 components; after entering the different shrinkage yarn preparation process, an improved process is adopted on the parallel drafting machine: the number of fibers in component A is 36, and the draft ratio The temperature of the hot plate is 110°C, the number of fibers in component B is 12, the draft ratio is 1.4 times, the temperature of the hot plate is 130°C, the number of fibers in component C is 12, and the draft ratio is 1.5 times. The temperature of the hot plate is 135°C, the number of fibers of component D is 12, the draft ratio is 1.8 times, the temperature of the hot plate is 140°C, the number of fibers of component E is 10, the draft ratio is 2.0 times, and the temperature of the hot plate is 150 ℃, the number of fibers in componen...
Embodiment 3
[0038] Nylon 6 coiled yarn is selected as the raw material. The core layer A and B components of the raw material are ordinary circular cross-section filaments, and the C components, D components, E components, and F components adopt trilobal cross-sections. Filament, G component, H component, I component, J component, using pentagonal cross-section filament, a total of 10 components; after entering the different shrinkage yarn preparation process, the improved process on the parallel drafting machine is as follows: The number of fibers in component A is 36, the draft ratio is 1.6 times, the temperature of the hot plate is 100°C, the number of fibers in component B is 24, the draft ratio is 1.8 times, the temperature of the hot plate is 110°C, and the fiber of component C is The number of fibers is 12, the draft ratio is 2.0 times, the hot plate temperature is 130°C, the number of D component fibers is 12, the draft ratio is 2.4 times, the hot plate temperature is 135°C, and th...
PUM
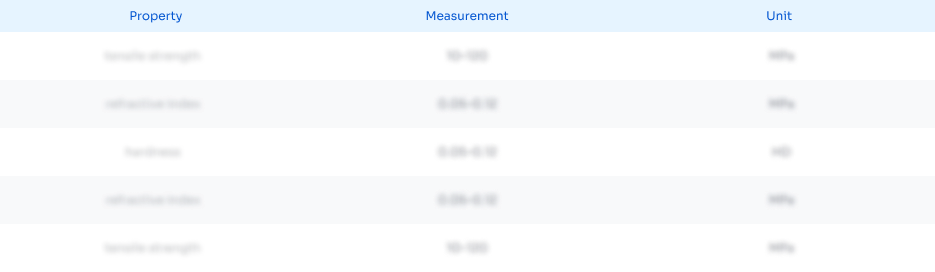
Abstract
Description
Claims
Application Information

- R&D Engineer
- R&D Manager
- IP Professional
- Industry Leading Data Capabilities
- Powerful AI technology
- Patent DNA Extraction
Browse by: Latest US Patents, China's latest patents, Technical Efficacy Thesaurus, Application Domain, Technology Topic, Popular Technical Reports.
© 2024 PatSnap. All rights reserved.Legal|Privacy policy|Modern Slavery Act Transparency Statement|Sitemap|About US| Contact US: help@patsnap.com