Multi-cycle, engine braking with positive power valve actuation control system and process for using the same
a technology of positive power valve actuation and control system, which is applied in the direction of machine/engine, charge feed system, valve arrangement, etc., can solve the problems of braking affecting the performance of engine braking, other internal combustion engine limitations, and inherent limitations of conventional single-cycle engine braking systems, so as to achieve reliable and robust performance, greater control and reliability
- Summary
- Abstract
- Description
- Claims
- Application Information
AI Technical Summary
Benefits of technology
Problems solved by technology
Method used
Image
Examples
Embodiment Construction
[0087]Reference will now be made in detail to a preferred embodiment of the present invention, an example of which is illustrated in the accompanying drawings. FIG. 4 and FIG. 18 illustrate a schematic view of the valve side of dual cam shafta rocker arm arrangement and dedicated brake cam rocker for a compression release-type engine brake assembly 10 according to the present invention. The compression release engine brake components and the valve actuation components are located in rocker arms 100, 200, and 300.
[0088]The rocker arms 100, 200, and 300 are spaced along a common rocker shaft 11 having at least one passage. The common rocker shaft 11 has a passage 12 through which a supply of engine oil flows therethrough, as shown in FIG. 56. The common rocker shaft 11 also has a supply passage 13 which supplies hydraulic fluid to an exhaust rocker arm 100 and an intake rocker arm 200. A valve 30 is located on the common rocker shaft 11, as shown in FIG. 56. The valve 30 is preferably...
PUM
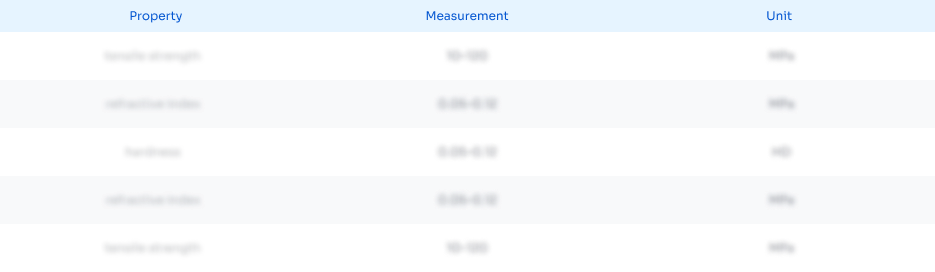
Abstract
Description
Claims
Application Information

- R&D
- Intellectual Property
- Life Sciences
- Materials
- Tech Scout
- Unparalleled Data Quality
- Higher Quality Content
- 60% Fewer Hallucinations
Browse by: Latest US Patents, China's latest patents, Technical Efficacy Thesaurus, Application Domain, Technology Topic, Popular Technical Reports.
© 2025 PatSnap. All rights reserved.Legal|Privacy policy|Modern Slavery Act Transparency Statement|Sitemap|About US| Contact US: help@patsnap.com