Engine control device
a control device and engine technology, applied in electrical control, multi-programming arrangements, electrical control, etc., can solve the problems of significant differences in electric power consumption, insufficient processing capacity of multi-core processors, and insufficient single-core processors used in conventional engine control devices. the effect of reducing the difference between communication delay times among the cores and reducing the communication delay time itsel
- Summary
- Abstract
- Description
- Claims
- Application Information
AI Technical Summary
Benefits of technology
Problems solved by technology
Method used
Image
Examples
Embodiment Construction
[0036]An engine control device according to an embodiment of the present invention is described hereunder with reference to the accompanying drawings.
[0037]An engine control device to which the present invention is applied is a device that calculates control target values of actuators involved in engine control using a multi-core processor. In the present invention, there is no limitation with respect to the kind or structure of an automobile engine controlled by the engine control device, and there is also no limitation with respect to the kind or number of actuators. For example, the engine control device of the present embodiment may be a control device for a gasoline engine. In such case, the engine control device calculates control target values of actuators such as a throttle, an ignition device, an injector, an EGR valve, a variable valve mechanism and a waste gate valve. The engine control device of the present embodiment may also be a control device for a diesel engine. In ...
PUM
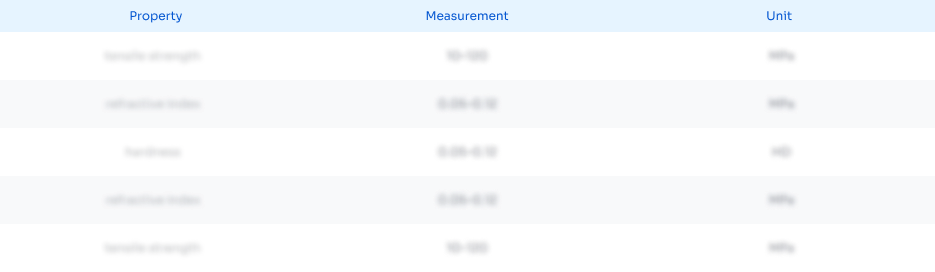
Abstract
Description
Claims
Application Information

- R&D
- Intellectual Property
- Life Sciences
- Materials
- Tech Scout
- Unparalleled Data Quality
- Higher Quality Content
- 60% Fewer Hallucinations
Browse by: Latest US Patents, China's latest patents, Technical Efficacy Thesaurus, Application Domain, Technology Topic, Popular Technical Reports.
© 2025 PatSnap. All rights reserved.Legal|Privacy policy|Modern Slavery Act Transparency Statement|Sitemap|About US| Contact US: help@patsnap.com