Multi-layer electronic component and method for manufacturing the same, multi-layer piezoelectric element
a piezoelectric element and electronic component technology, applied in piezoelectric/electrostrictive/magnetostrictive devices, piezoelectric/electrostriction/magnetostriction machines, electrical apparatuses, etc., can solve the problems of reducing the piezoelectric displacement, affecting the stability of the piezoelectric element, etc., to achieve excellent durability, increase the bonding strength, and suppress delamination
- Summary
- Abstract
- Description
- Claims
- Application Information
AI Technical Summary
Benefits of technology
Problems solved by technology
Method used
Image
Examples
first embodiment
[0056]FIG. 1 is a longitudinal sectional view showing the constitution of a multi-layer electronic component (multi-layer piezoelectric actuator) according to the first embodiment of the present invention.
[0057]The multi-layer electronic component of the first embodiment has a column-like stack 3 of a rectangular prism shape comprising an active section 8 formed by stacking a plurality of ceramic layers 1 and a plurality of internal electrodes 2 alternately one on another, and inactive sections 9 provided on both ends of the active section 8 in the direction of stacking, as shown in FIG. 1.
[0058]The ceramic layer 1 is made of a piezoelectric ceramic material of which main component is lead zirconate titanate Pb(Zr, Ti)O3 (hereinafter abbreviated as PZT) or barium titanate BaTiO3, for example, but is not limited to this composition and may be made of any ceramic material that has piezoelectric property. The piezoelectric material preferably has a high value of piezoelectric strain co...
second embodiment
[0085]The multi-layer piezoelectric element according to the second embodiment of the present invention will be described in detail below.
[0086]FIG. 6A is a perspective view showing the structure of a multi-layer piezoelectric element according to the second embodiment. FIG. 6B is an exploded perspective view of the inner structure of the multi-layer piezoelectric element according to the second embodiment, showing the stacked structure of the piezoelectric layers and the internal electrodes.
[0087]In the multi-layer piezoelectric element according to the second embodiment, as shown in FIG. 6A, B, external electrodes 15 are connected so as to establish electrical continuity with the ends of the internal electrodes 12 that are exposed in every other layer on a pair of opposing side faces of the stack 13 that is formed by alternately stacking the piezoelectric layers 11 and the internal electrodes 12 one on another. Layers on both ends in the stacking direction of the stack 13 are the ...
third embodiment
[0144]The piezoelectric electronic component according to the third embodiment of the present invention is a multi-layer piezoelectric actuator of similar constitution as that of the first embodiment, with a part of the manufacturing process different from that of the first embodiment.
[0145]FIG. 9 is an enlarged sectional view of a part of the multi-layer piezoelectric actuator of the third embodiment, with similar components identified with similar reference numerals as in the first embodiment.
[0146]Thickness of the piezoelectric layer 1, namely the distance between the internal electrodes 2, is preferably not larger than 200 μm, or more preferably not larger than 150 μm, in order to make the construction smaller and apply high electric field. On the other hand, thickness of the piezoelectric layer 1 is set not smaller than 50 μm, preferably not smaller than 70 μm, in order to reduce the transient time of applying a voltage to the piezoelectric layer 1 and enable faster response. T...
PUM
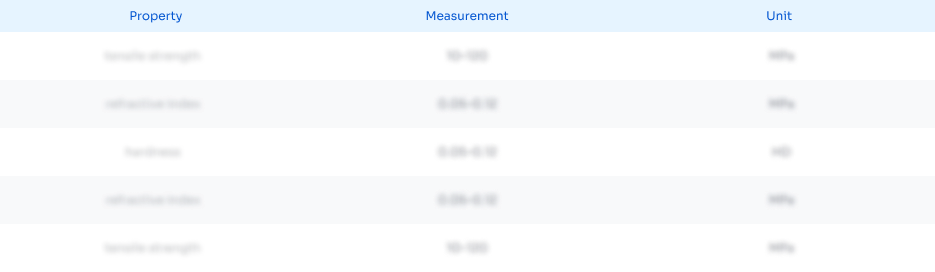
Abstract
Description
Claims
Application Information

- R&D
- Intellectual Property
- Life Sciences
- Materials
- Tech Scout
- Unparalleled Data Quality
- Higher Quality Content
- 60% Fewer Hallucinations
Browse by: Latest US Patents, China's latest patents, Technical Efficacy Thesaurus, Application Domain, Technology Topic, Popular Technical Reports.
© 2025 PatSnap. All rights reserved.Legal|Privacy policy|Modern Slavery Act Transparency Statement|Sitemap|About US| Contact US: help@patsnap.com