Vane type hydraulic actuator
a hydraulic actuator and valve body technology, applied in the direction of valve arrangement, oscillating piston engine, machine/engine, etc., can solve the problems of high production cost, low productivity, complex apparatus, etc., and achieve the effect of reducing production cost and improving productivity
- Summary
- Abstract
- Description
- Claims
- Application Information
AI Technical Summary
Benefits of technology
Problems solved by technology
Method used
Image
Examples
embodiment 1
The embodiment 1 is explained below, referring to FIGS. 1-9.
The elements identical or equivalent with the elements in the explanation of the prior art are referred by the same reference numerals, and their explanation is omitted.
Reference numeral 1 denotes a chip seal as a sealing element. The chip seal 1 is formed as a substantially square prism. Perspective views of the chip seal are shown in FIG. 5. The chip seal 1 can have a recessing portion 1a at its bottom. And its both end portions can be chamfered, as shown in FIG. 5(a). However, the chip seal 1 can be a simple square prism bar having no recessing portion, as shown in FIG. 5(b).
Reference numeral 2 denotes a seal groove for receiving the chip seal. The seal groove 2 is disposed at the tip of each vane 64-67. Perspective view of the seal groove and the chip seal received in it are shown in FIG. 3. The groove can be parallel with the rotor axis, namely the width can be constant, as shown in FIG. 3(b). However, the groove can b...
embodiment 2
The explained, supposing that the chip seal 1 has a recessing portion 1a. However, the recessing portion 1a is not inevitable for the chip seal 1.
Embodiment 3
The embodiment 3 is explained below, referring to FIGS. 18-22.
The chip seal 1 has a hollow portion 1c at its bottom side, so that the center of the gravity of the chip seal 1 as well as the oil pressure acting plane become nearer to the inner surface of the case 43. The structure of the other part of the hydraulic actuator of this embodiment is identical to that of the embodiment 2, thus their explanation is omitted here for avoiding the redundancy.
The function of the chip seal according to the embodiment 3:
The essential functions are similar to that of the embodiment 2. The different point is that the oil pressure acting plane becomes nearer to the inner surface of the case 43, because the working oil can enter into the hollow portion 1c at the bottom portion of the chip seal. The acting plane of the force to displace the chip...
embodiment 3
The explained, supposing that the chip seal 1 has a shape shown in FIG. 18, however the shape of the chip seal 1 is not limited to this form. For example, the chip seal 1 may have a hollow portion 1c at its bottom as well as a concave recessing portion 1d at its side surface, as shown in FIG. 22. Also, such a chip seal has effects similar to that of ship seal shown in FIG. 18. The working oil can flow easily into the hollow portion 1c through the concave recessing portion 1d, thus a stable sealing force can be promptly obtained and assured. The material cost for the chip seal can be reduced, without reducing the tolerable strength. However, it shall be noted that the hollow portion 1c is not inevitable. For example, the chip seal can have a shape as shown in FIG. 5(b).
An advantage of the present invention is that the sealing element can be pressed to the counter surface by the oil pressure, without using a supplemental pressing means, for example, a spring in the prior art. Therefor...
PUM
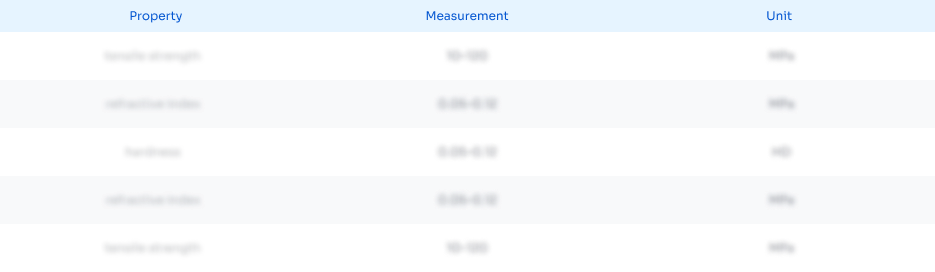
Abstract
Description
Claims
Application Information

- R&D
- Intellectual Property
- Life Sciences
- Materials
- Tech Scout
- Unparalleled Data Quality
- Higher Quality Content
- 60% Fewer Hallucinations
Browse by: Latest US Patents, China's latest patents, Technical Efficacy Thesaurus, Application Domain, Technology Topic, Popular Technical Reports.
© 2025 PatSnap. All rights reserved.Legal|Privacy policy|Modern Slavery Act Transparency Statement|Sitemap|About US| Contact US: help@patsnap.com