Systems and methods for producing ice
a technology of ice production and production methods, applied in the field of high-quality ice making, can solve the problems of simple molds, low quality of ice that comes out, and inconvenient use, and achieve the effects of reducing thermal resistance, reducing heat loss, and reducing was
- Summary
- Abstract
- Description
- Claims
- Application Information
AI Technical Summary
Benefits of technology
Problems solved by technology
Method used
Image
Examples
embodiments / improvements
Possible Future Embodiments / Improvements
[0174]In addition to the process considerations in designing ice machines in accordance with the principals of the present invention, implementations can employ additional elements and improvements. For example, a water reservoir could be integrated into the ice machine but removeable by the user. The user could fill up this reservoir and install in the ice machine. Then the ice machine could pump and / or direct water from the reservoir into the tray. This could help reduce process variability, allowing for a consistent fill each time with no need for water sensing or intervention by the user.
[0175]The output of a process of the present invention is not only clear ice, but also water concentrated with impurities (TDS and TDG) that must be purged. In the exemplary embodiment described herein, the user must take the tray and dump out the water to retrieve their ice. Alternatively, the ice machine could automatically remove the water from the tray...
PUM
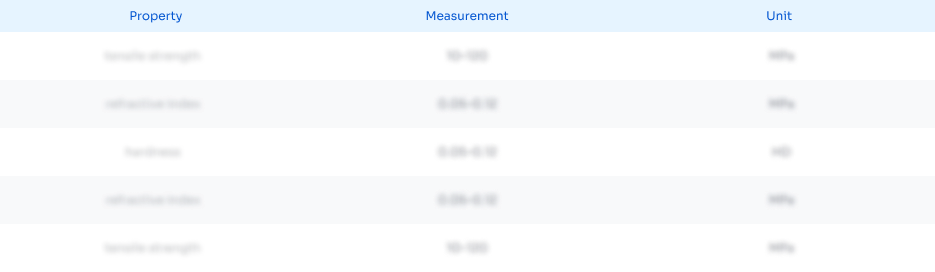
Abstract
Description
Claims
Application Information

- R&D
- Intellectual Property
- Life Sciences
- Materials
- Tech Scout
- Unparalleled Data Quality
- Higher Quality Content
- 60% Fewer Hallucinations
Browse by: Latest US Patents, China's latest patents, Technical Efficacy Thesaurus, Application Domain, Technology Topic, Popular Technical Reports.
© 2025 PatSnap. All rights reserved.Legal|Privacy policy|Modern Slavery Act Transparency Statement|Sitemap|About US| Contact US: help@patsnap.com