Production method of solid fuel
a production method and solid fuel technology, applied in the direction of solid fuels, petroleum industry, fuels, etc., can solve the problems of increased production cost, increased handling cost, and increased dust pollution, and achieve the effect of great strength
- Summary
- Abstract
- Description
- Claims
- Application Information
AI Technical Summary
Benefits of technology
Problems solved by technology
Method used
Image
Examples
example 1
[0067]First, a granular solid fuel was obtained by subjecting a mixture of a coal-derived powder fuel and a cohesive fine coal at a blending mass ratio of 85:10 to compression molding in a double-roll molding machine, the coal-derived powder fuel being powder of a modified coal obtained by thermally dehydrating a brown coal in oil, whereas the cohesive fine coal being a brown coal pulverized and then filtered through a sieve having a mesh opening size of 3 mm. The rotation frequency of the double-roll molding machine was adjusted such that a crushing strength of the solid fuel obtained was 0.7 MPa, which is a value required for a typical coal-based fuel briquette. It is to be noted that the bulk density of the coal-derived powder fuel was measured to be 0.52 g / cc. As the double-roll molding machine, “K205” available from Furukawa Industrial Machinery Systems Co., Ltd. was used, equipped with rolls provided with cavities each having a longitudinal diameter of 38 mm, a shortest diamet...
example 2
[0072]First, a mixture of the coal-derived powder fuel and the cohesive fine coal similar to those of Example 1 at a mass ratio of 70:10 was subjected to compression molding in the double-roll molding machine, with the rotation frequency of the double-roll molding machine being adjusted such that a crushing strength of the solid fuel obtained was 0.7 MPa.
[0073]The solid fuel thus obtained was pulverized and then filtered through a sieve having a mesh opening size of 10 mm to give a pulverized fuel, and a material mixture was obtained by blending the coal-derived powder fuel, the cohesive fine coal, and the pulverized fuel at a mass ratio of 70:10:20. The material mixture was subjected to compression molding in the double-roll molding machine, with the rotation frequency of the double-roll molding machine being adjusted such that a crushing strength of the solid fuel obtained was 0.7 MPa.
[0074]The solid fuel obtained by compression molding of the material mixture containing the pulve...
example 3
[0075]First, a mixture of the coal-derived powder fuel and the cohesive fine coal similar to those of Example 1 at a mass ratio of 60:20 was subjected to compression molding in the double-roll molding machine, with the rotation frequency of the double-roll molding machine being adjusted such that a crushing strength of the solid fuel obtained was 0.7 MPa.
[0076]The solid fuel thus obtained was pulverized and then filtered through a sieve having a mesh opening size of 10 mm to give a pulverized fuel, and a material mixture was obtained by blending the coal-derived powder fuel, the cohesive fine coal, and the pulverized fuel at a mass ratio of 60:20:20. The material mixture was subjected to compression molding in the double-roll molding machine, with the rotation frequency of the double-roll molding machine being adjusted such that a crushing strength of the solid fuel obtained was 0.7 MPa.
[0077]The solid fuel obtained by compression molding of the material mixture containing the pulve...
PUM
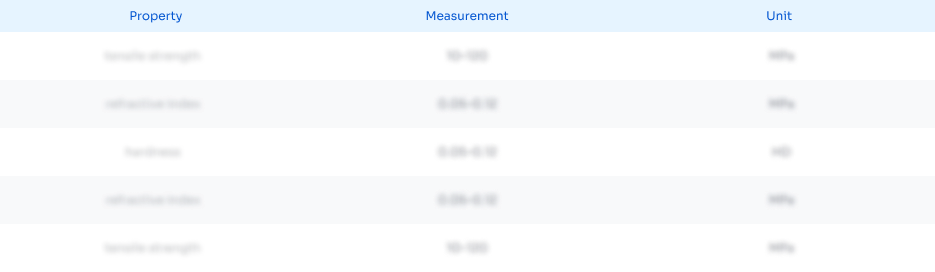
Abstract
Description
Claims
Application Information

- R&D
- Intellectual Property
- Life Sciences
- Materials
- Tech Scout
- Unparalleled Data Quality
- Higher Quality Content
- 60% Fewer Hallucinations
Browse by: Latest US Patents, China's latest patents, Technical Efficacy Thesaurus, Application Domain, Technology Topic, Popular Technical Reports.
© 2025 PatSnap. All rights reserved.Legal|Privacy policy|Modern Slavery Act Transparency Statement|Sitemap|About US| Contact US: help@patsnap.com