Rotary mill
a rotary mill and milling machine technology, applied in the field of rotary mills, can solve the problems of post-operative pain, damage to bearings, and more demanding design requirements for partial knee replacement prostheses than for total knee replacement prostheses, and achieve the effect of facilitating accuracy and repeatability of milling
- Summary
- Abstract
- Description
- Claims
- Application Information
AI Technical Summary
Benefits of technology
Problems solved by technology
Method used
Image
Examples
Embodiment Construction
[0063]With reference to FIGS. 2 to 4, a rotary mill 2 comprises a body portion 4 and a guide portion 6. The body portion 4 comprises a rotary body 8 that terminates at one end in an annular milling surface 10. The milling surface comprises a series of milling teeth 12 that extend from the surface 10. In the illustrated embodiment, the milling surface 10 is formed on an annular shoulder 14 that protrudes outwardly from the rotary body 8. An abutment surface 15 extends radially inwardly of the projecting milling surface 10. At a second end of the rotary body 8 an integral shank 16 extends along an axis of rotation 18 of the rotary body. The shank 16 is suitable for attachment to the chuck of a surgical drill (not shown). A bore 20 extends through the rotary body 8 along the axis of rotation 18 of the rotary body 8.
[0064]The guide portion 6 comprises a guide body 22 and a guide peg 24. The guide body 22 comprises a trail unicondylar femoral prosthesis component. The guide body thus com...
PUM
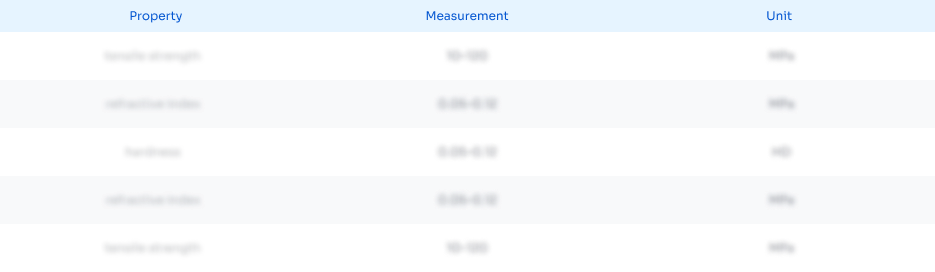
Abstract
Description
Claims
Application Information

- Generate Ideas
- Intellectual Property
- Life Sciences
- Materials
- Tech Scout
- Unparalleled Data Quality
- Higher Quality Content
- 60% Fewer Hallucinations
Browse by: Latest US Patents, China's latest patents, Technical Efficacy Thesaurus, Application Domain, Technology Topic, Popular Technical Reports.
© 2025 PatSnap. All rights reserved.Legal|Privacy policy|Modern Slavery Act Transparency Statement|Sitemap|About US| Contact US: help@patsnap.com