Pre-Cooling of Natural Gas by High Pressure Compression and Expansion
a compression expansion and high pressure technology, applied in the field of liquefaction of natural gas, can solve the problems of increasing the loss prevention issue of flng, significant technical challenges remain in the application of the technology, and the capacity limitation of the smr process
- Summary
- Abstract
- Description
- Claims
- Application Information
AI Technical Summary
Benefits of technology
Problems solved by technology
Method used
Image
Examples
Embodiment Construction
[0025]Various specific aspects, embodiments, and versions will now be described, including definitions adopted herein. Those skilled in the art will appreciate that such aspects, embodiments, and versions are exemplary only, and that the invention can be practiced in other ways. Any reference to the “invention” may refer to one or more, but not necessarily all, of the embodiments defined by the claims. The use of headings is for purposes of convenience only and does not limit the scope of the present invention. For purposes of clarity and brevity, similar reference numbers in the several Figures represent similar items, steps, or structures and may not be described in detail in every Figure.
[0026]All numerical values within the detailed description and the claims herein are modified by “about” or “approximately” the indicated value, and take into account experimental error and variations that would be expected by a person having ordinary skill in the art.
[0027]As used herein, the te...
PUM
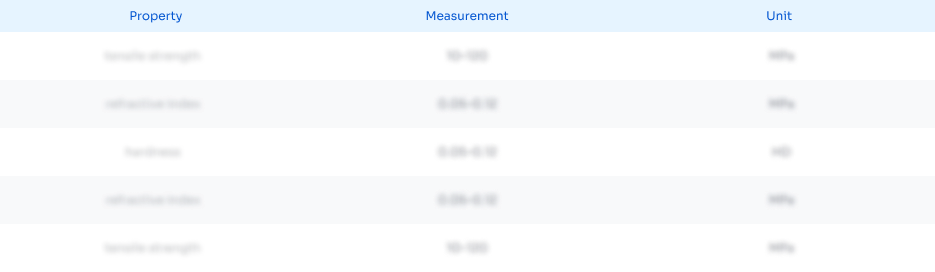
Abstract
Description
Claims
Application Information

- R&D
- Intellectual Property
- Life Sciences
- Materials
- Tech Scout
- Unparalleled Data Quality
- Higher Quality Content
- 60% Fewer Hallucinations
Browse by: Latest US Patents, China's latest patents, Technical Efficacy Thesaurus, Application Domain, Technology Topic, Popular Technical Reports.
© 2025 PatSnap. All rights reserved.Legal|Privacy policy|Modern Slavery Act Transparency Statement|Sitemap|About US| Contact US: help@patsnap.com