Method of Co-Firing Coal or Oil with a Gaseous Fuel in a Furnace
a gaseous fuel and co-fire technology, which is applied in the direction of machines/engines, lighting and heating apparatus, combustion types, etc., can solve the problem of purposely limited combustion of gaseous fuel, and achieve the effect of safe burning, easy burning, and safe combustion
- Summary
- Abstract
- Description
- Claims
- Application Information
AI Technical Summary
Benefits of technology
Problems solved by technology
Method used
Image
Examples
Embodiment Construction
[0029]A typical coal fired boiler has several burners into which pulverized coal in a stream of air is injected into a flame zone. Natural gas, i.e. methane, is separately injected into the burner. The gas injection may be accomplished through gas igniter tubes, or through separate higher velocity injector piping tips, spuds or nozzles. Normal igniter operation is shown in FIG. 1, where the igniter establishes its own stable flame structure, which then impinges on the main condensed phase fuel stream as it heats-up and mixes with its dedicated burner air supply. As can be seen in FIG. 1, a typical swirl type burner 1 is provided on the wall 2 of a boiler. The burner 1 has an opening 4 in which there is an injector tube 6 through which a stream of pulverized coal 5 is injected. Swirling combustion air 7 is injected through the opening 4 around the injector tube 6. Typically the combustion air is injected at a different velocity than the pulverized coal. An igniter tube 8 is positione...
PUM
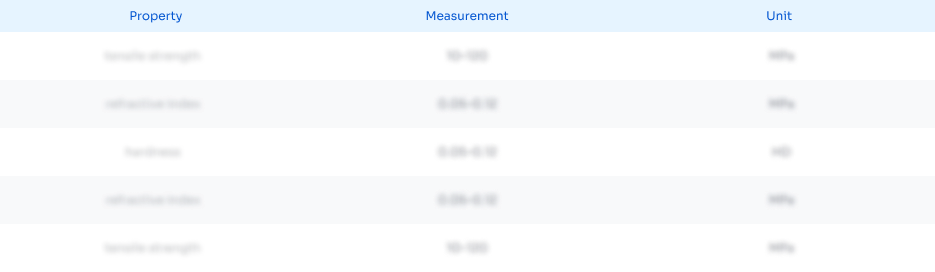
Abstract
Description
Claims
Application Information

- R&D
- Intellectual Property
- Life Sciences
- Materials
- Tech Scout
- Unparalleled Data Quality
- Higher Quality Content
- 60% Fewer Hallucinations
Browse by: Latest US Patents, China's latest patents, Technical Efficacy Thesaurus, Application Domain, Technology Topic, Popular Technical Reports.
© 2025 PatSnap. All rights reserved.Legal|Privacy policy|Modern Slavery Act Transparency Statement|Sitemap|About US| Contact US: help@patsnap.com